Case study
Plastic packaging manufacturer improves quality and OEE using Guidewheel
Updated:
March 27, 2024
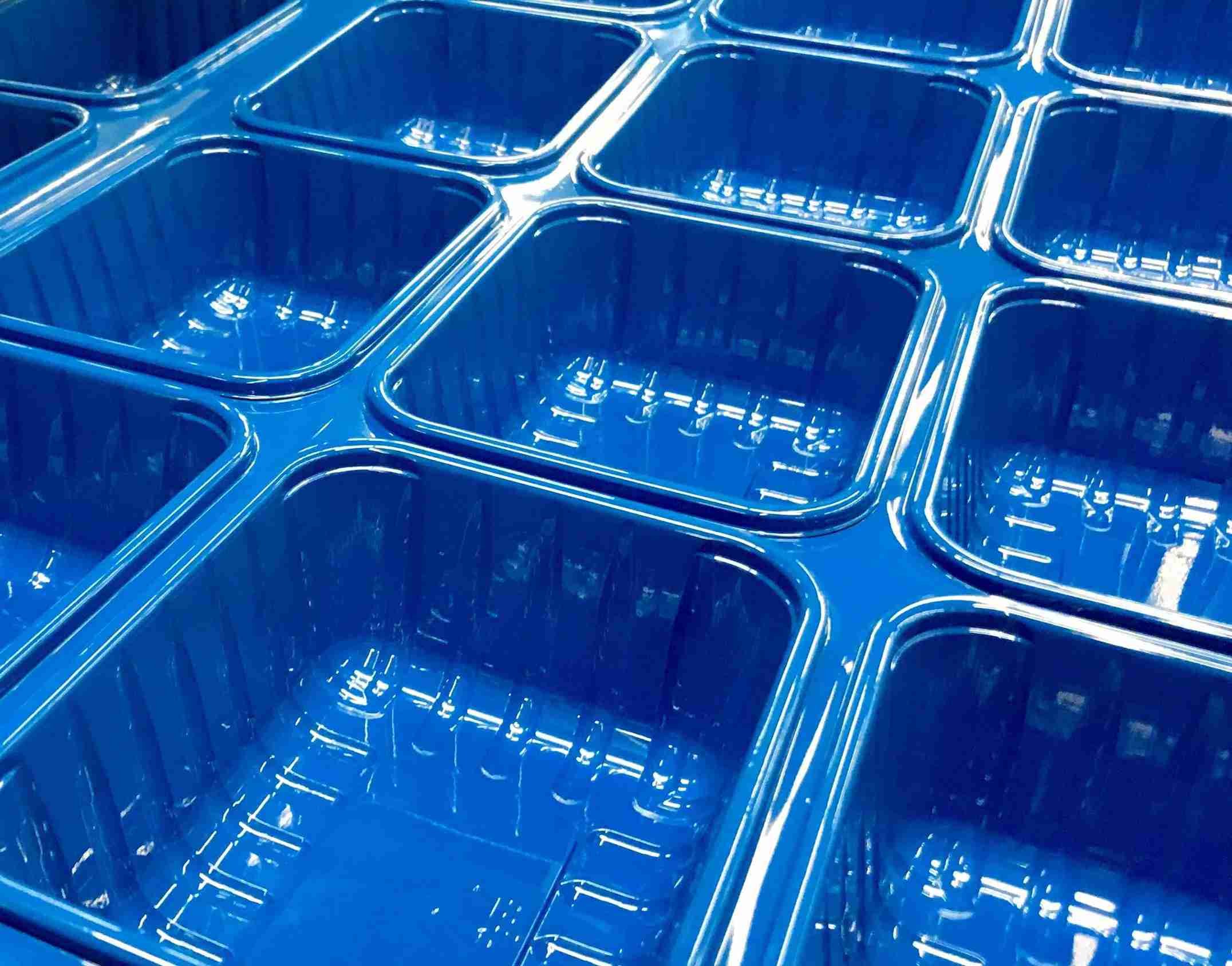
Industry: Plastic packaging thermoformer
Size: 1,000+ employees
Manufacturing locations: 6
Operating six facilities across two countries, this manufacturer is one of the largest plastic packaging thermoformers in North America. Dedicated to being a global leader in the innovative design and manufacturing of rigid food containers and versatile food service cling film, their commitment extends to enhancing sustainability through the use of eco-friendly materials.
Ensuring uninterrupted production is paramount for this operation that runs 24/7. Recognizing the high cost of downtime, the company emphasizes Overall Equipment Effectiveness (OEE) to reliably meet customer demands. Monitoring this metric fosters awareness, execution, and improvement across the operation. However, for years, the process of collecting data for OEE calculations proved cumbersome and error-prone.
Previously, operators filled out checklists throughout their shifts to document issues, a method that led to after-the-fact reporting and often provided an inaccurate snapshot of the day's events. Their Director of Quality and Process Excellence noted the challenges:
"If operators missed production targets, they'd have to backtrack through checklists to identify downtime issues. It was a lot of after-the-fact reporting, and we lacked confidence in its accuracy."
To address these issues, the team sought a real-time, automated system for accurate OEE data collection that would empower every team member to proactively manage machine performance. They chose Guidewheel for its easy installation and rapid time-to-value. Guidewheel now provides real-time visibility into machine performance across the team. The Guidewheel Scoreboard, displayed throughout the facility, helps the team to track performance and identify opportunities for improvement. Supervisors use Guidewheel to code downtime events, enabling them to pinpoint root causes and quickly take corrective actions. The Director of Quality and Process Excellence highlights the impact:
"Now that we're capturing granular data, we gain valuable insights into our operations. Guidewheel helps us take our OEE improvements to the next level, identifying which lines, products, and shifts require attention. For instance, we've discovered a correlation between downtime events and an increase in non-conforming products. With Guidewheel, I'm alerted whenever a machine goes down, allowing us to prevent non-conforming material from reaching the customer."
Guidewheel has become an indispensable part of this manufacturer's continuous improvement program. Armed with reliable, granular data, the company can strategically focus on initiatives with the greatest potential impact, advancing their mission to innovate on behalf of their customers.