Unlock compounding performance over time
Drive higher output, stronger margins, and continuous improvement as your operations scale.
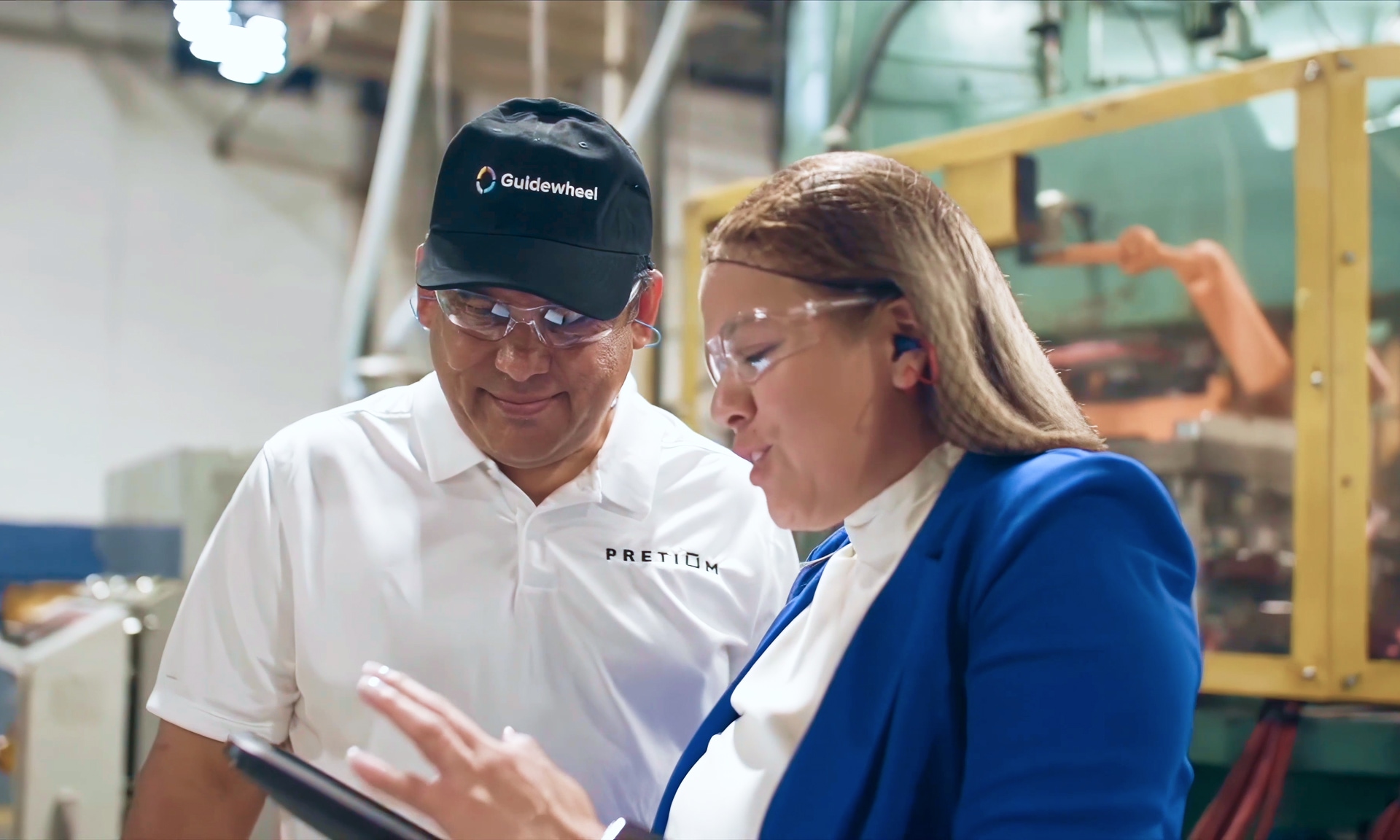
Trusted by hundreds
of leading manufacturers
From disconnected tools to a system that scales with you
Most traditional systems require a heavy lift for little return, especially when scaling across lines and plants.
Guidewheel makes it easy to scale what works. Every additional machine, user, or site adds more value, surfaces new opportunities, and drives performance across your entire operation.
Build a foundation for continuous improvement
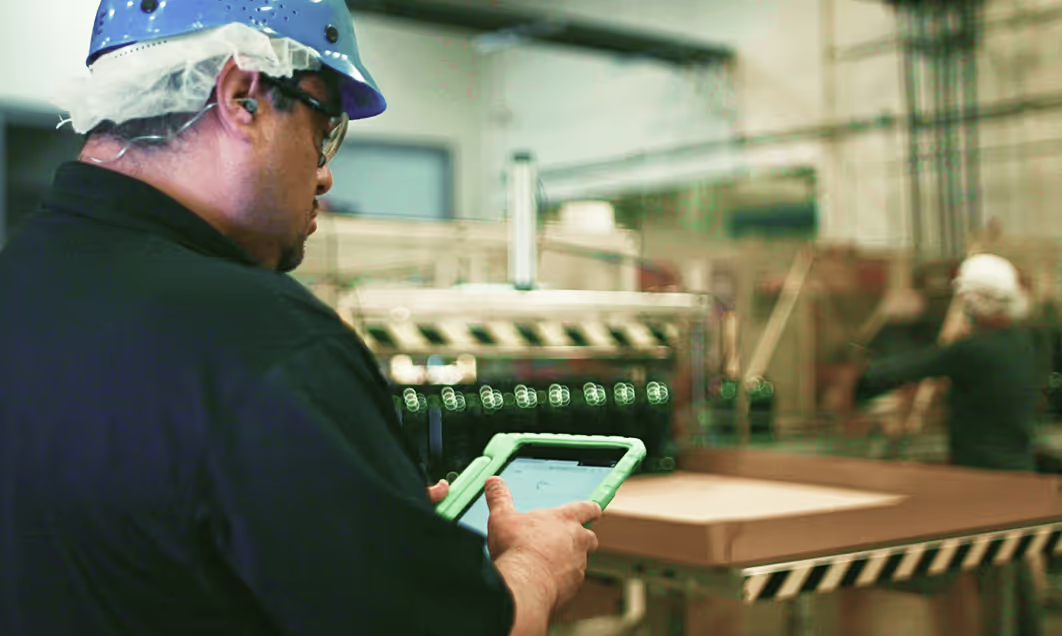
Build a real-time intelligence layer
Connect your equipment, teams, and sites in one system to surface insights, share knowledge, and improve every day.
Get smarter with every step
Layer on AI and anomaly detection to catch issues before they escalate and drive continuous improvement across your operations.
.avif)
.avif)
Expand visibility across your operations
Add sensors and integrations over time to expand what you can monitor, without adding complexity or overhead.
Make excellence repeatable
Bring best practices and tribal knowledge into repeatable, scalable systems that keep performance high even as teams grow or change.
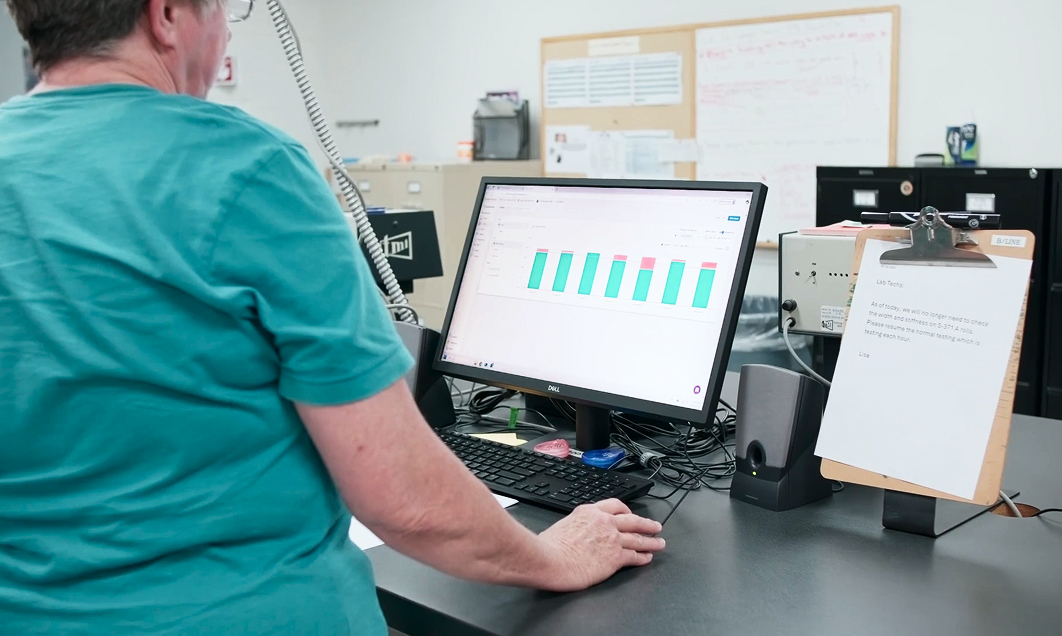
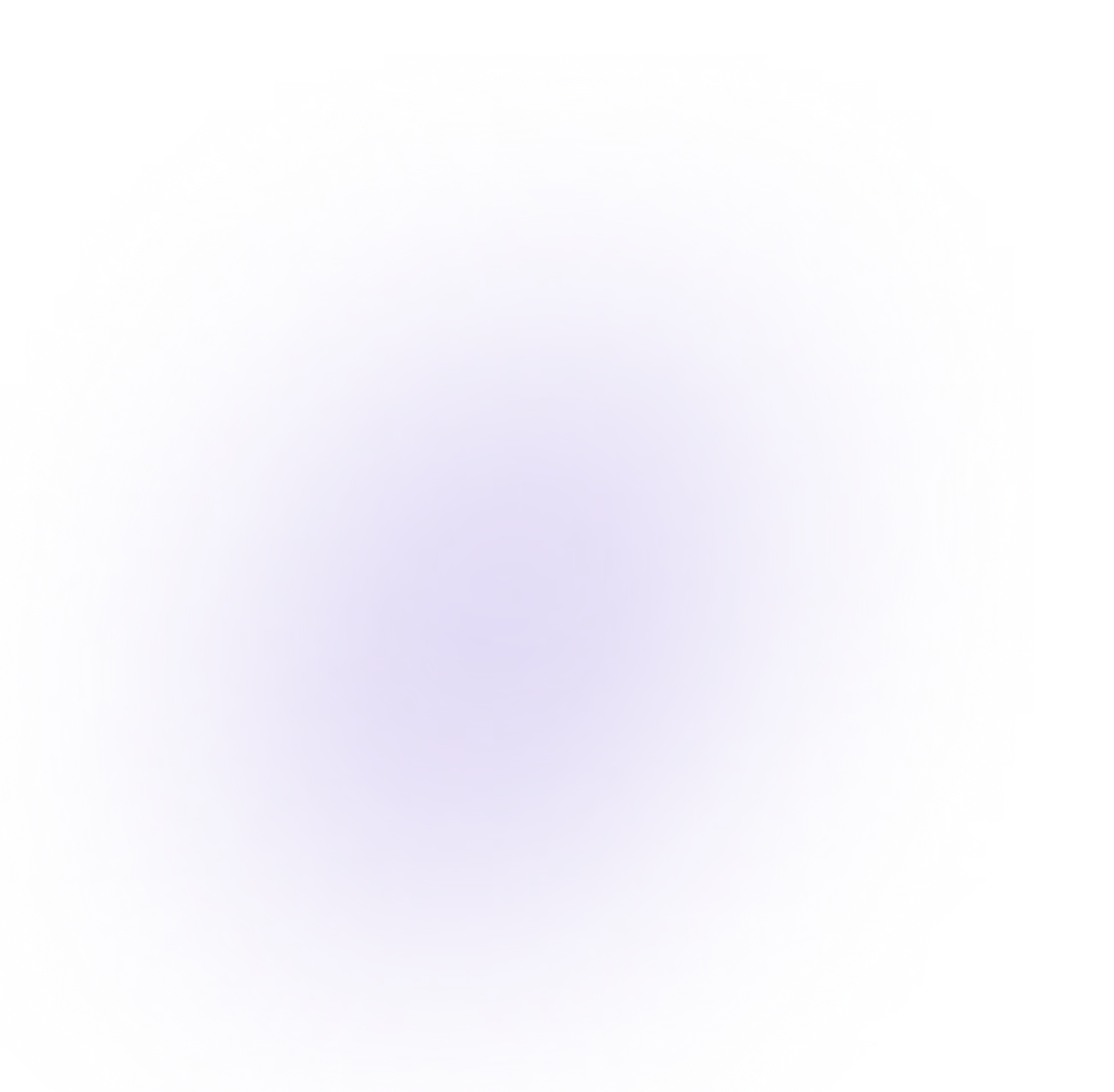
16% improvement in energy efficiency at Pretium
Guidewheel helped Pretium cut waste and automate energy tracking, while tying insights into their carbon accounting, unlocking measurable efficiency gains and a stronger foundation for sustainability.
AI-Powered Anomaly Detection
Stay ahead of failures by spotting unusual patterns in machine behavior, before they turn into bigger problems.
- Detect subtle shifts that operators might miss
- Get early warnings of performance or quality issues
- Prevent problems before they disrupt production
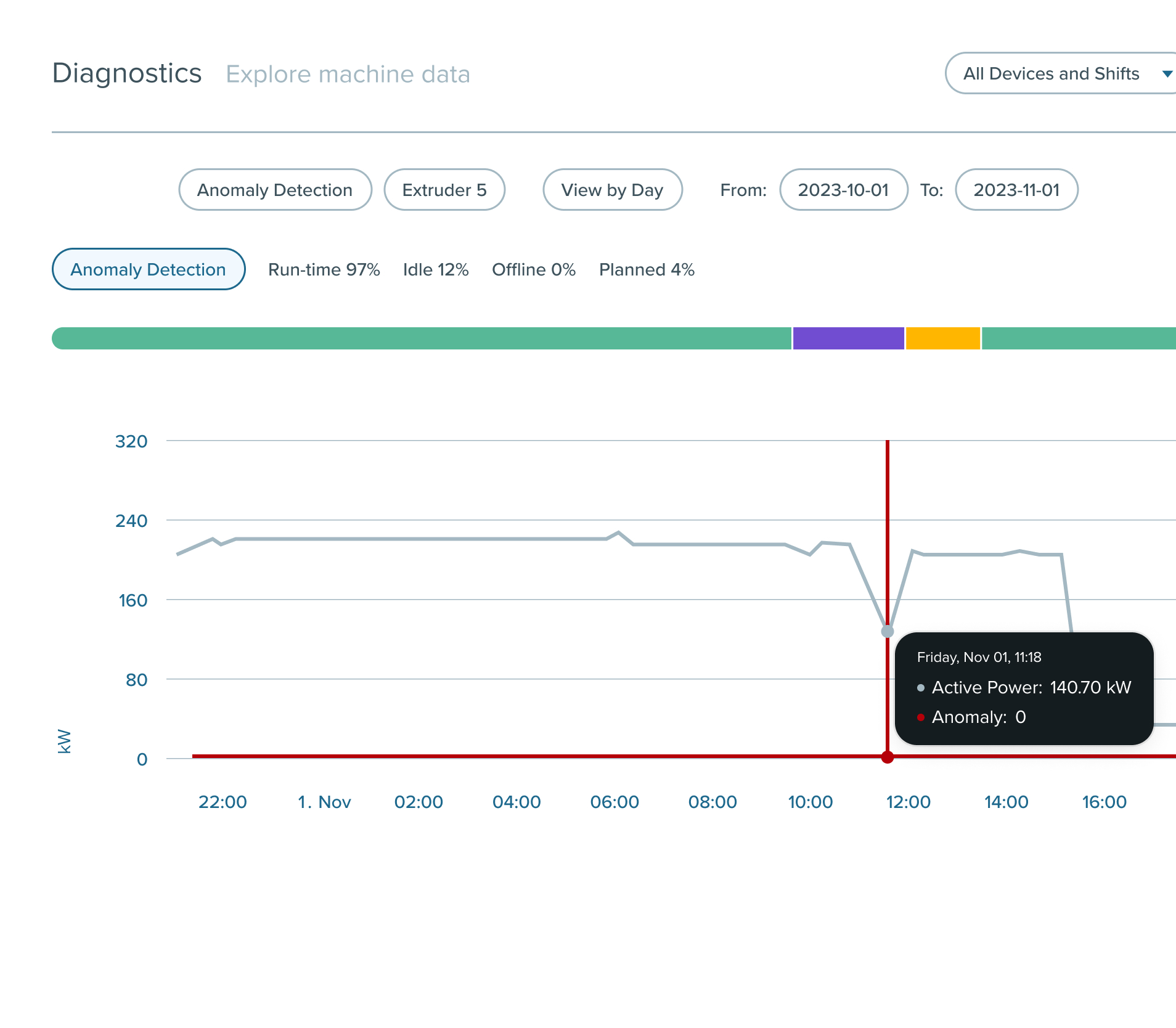
FactoryOps Hub
Bring your most important production data, like runtime, OEE, and more, into one centralized view to drive alignment and action.
- Track performance across machines, shifts, and plants
- Share key insights during meetings or reviews
- Guide teams with a single source of truth
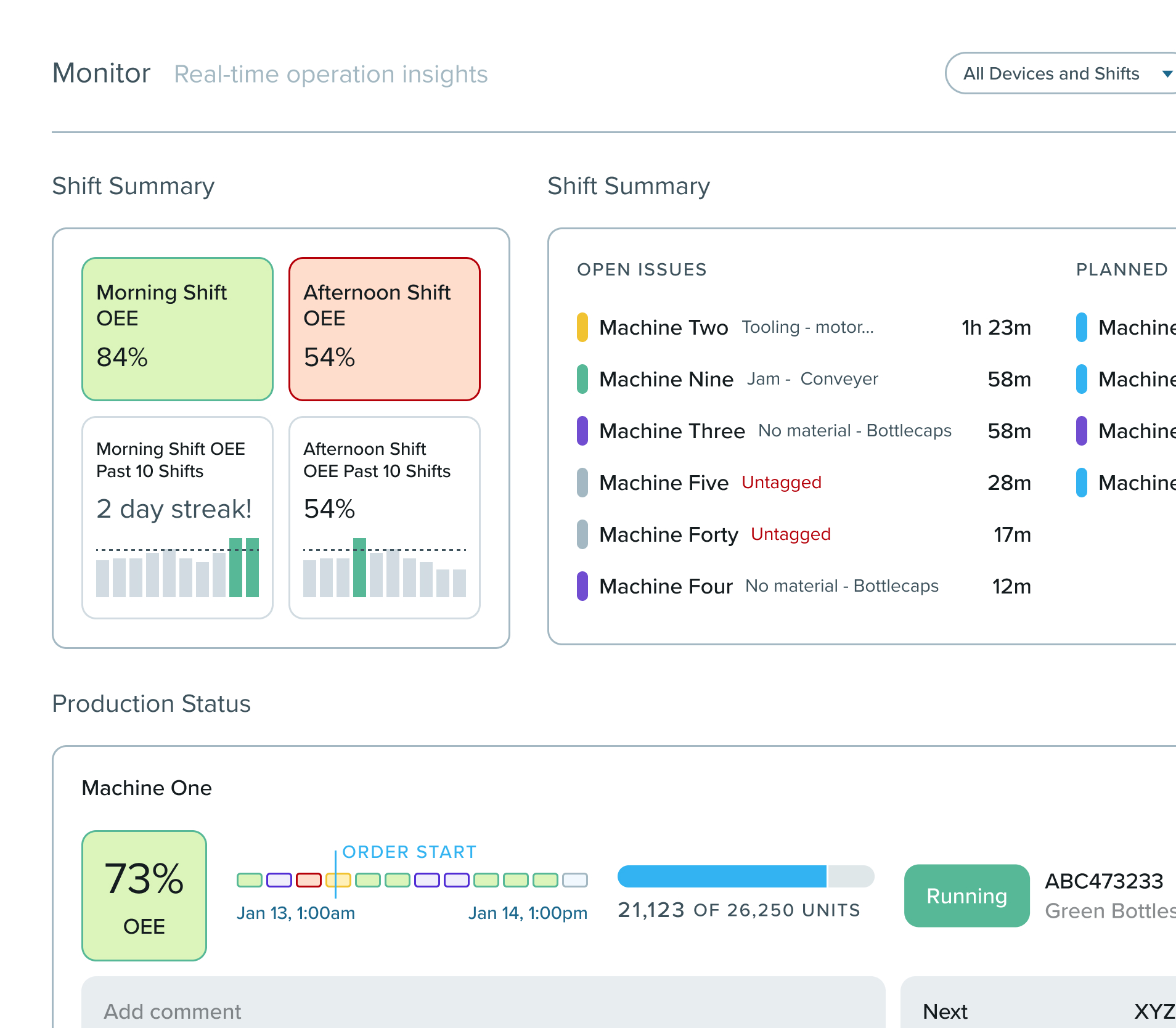
Energy Monitoring
Track energy usage and cost across every machine to reduce waste and improve efficiency.
- Monitor energy consumption in real time
- Tie usage and cost data into performance analysis
- Identify opportunities to reduce waste and lower cost per unit
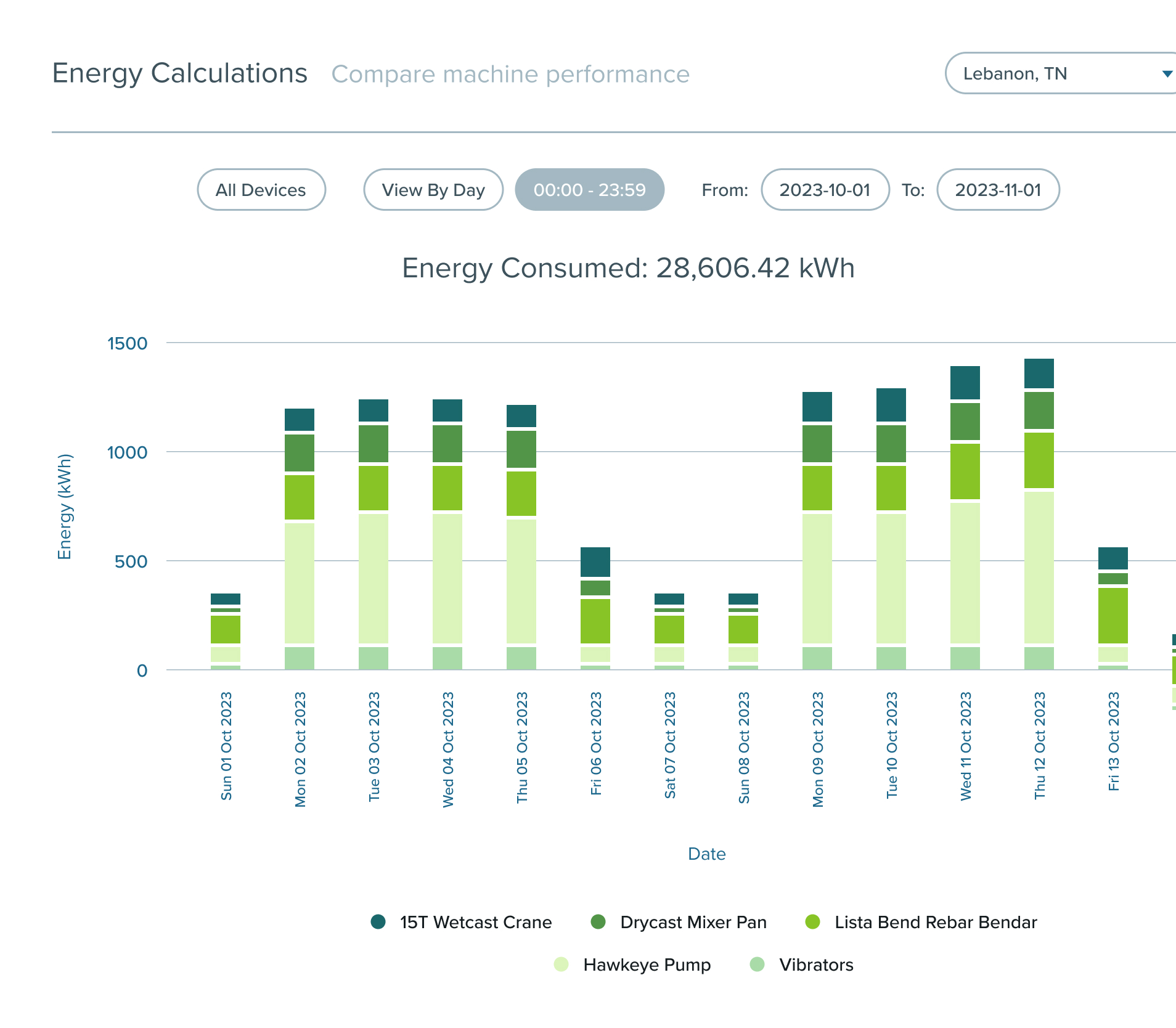
Additional Sensors
Layer on more data sources, like parts counting, temperature, and more, to unlock deeper insights where they matter most.
- Monitor inputs and outputs beyond runtime
- Expand visibility into more steps of production
- Support targeted improvements across processes
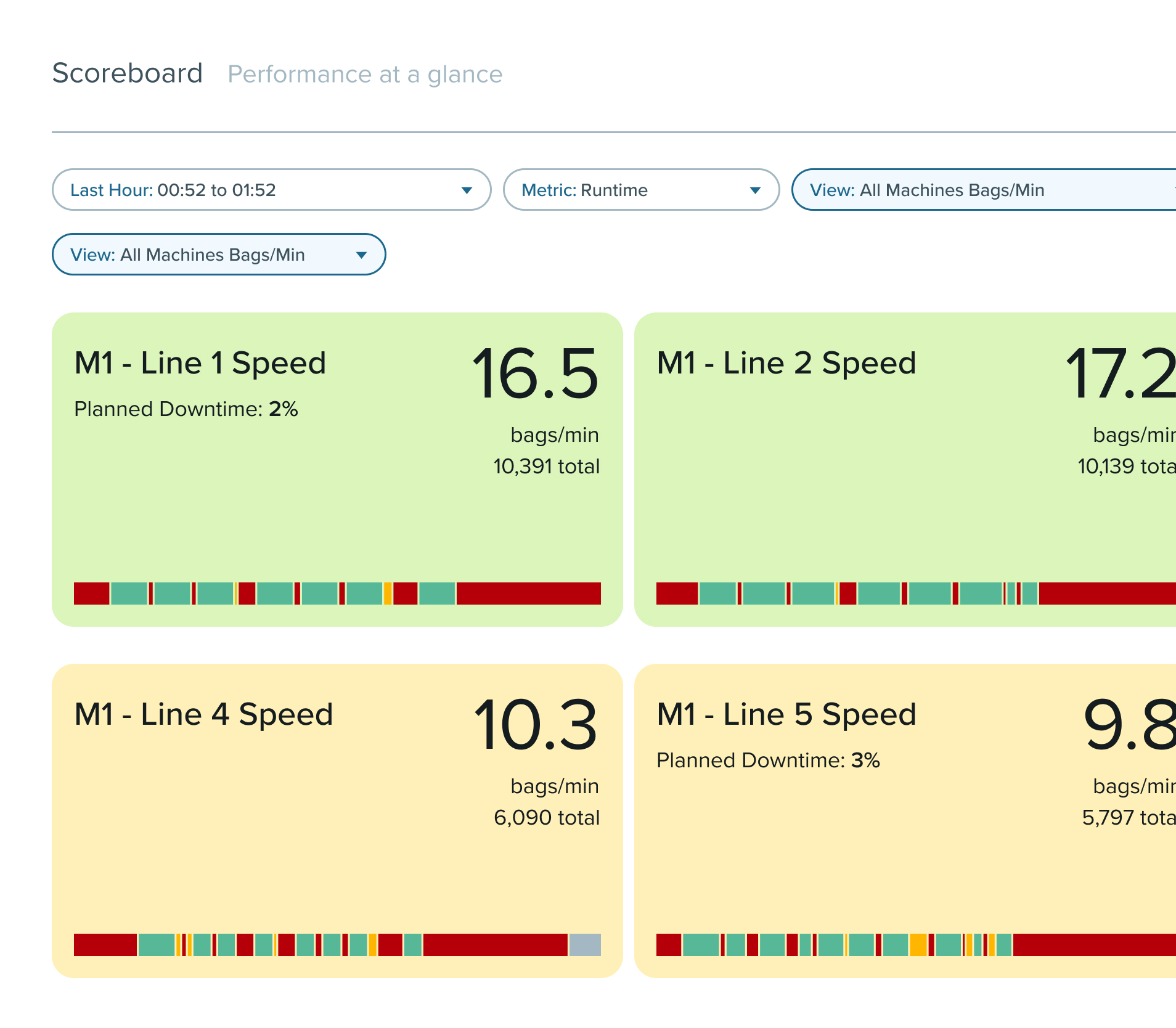
Integrations
Connect Guidewheel to the tools you already use, either natively or through our open API, to streamline data flow and enhance visibility.
- Sync with ERPs, MES, and maintenance systems
- Eliminate data silos across departments
- Build a connected system that scales with you
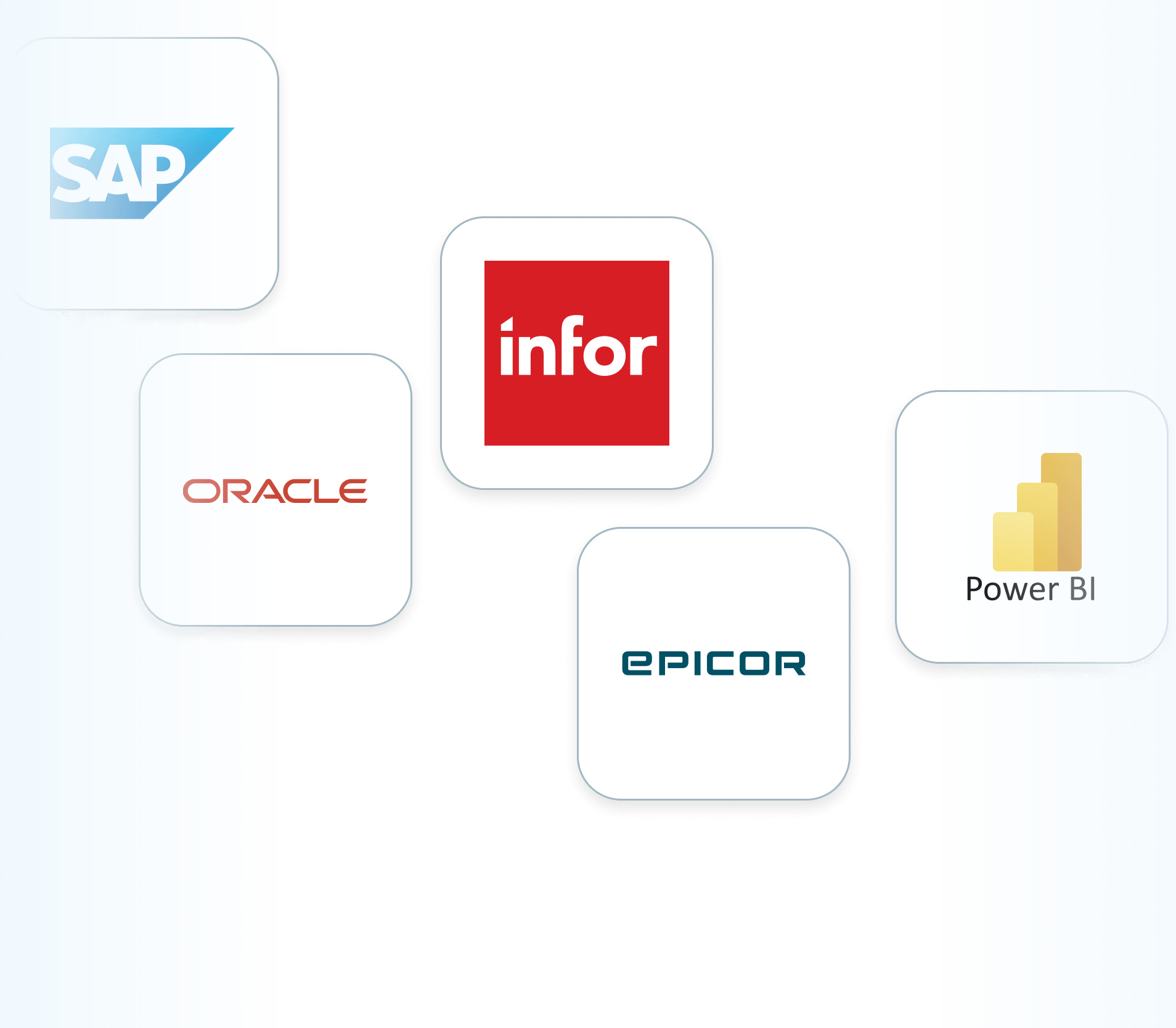
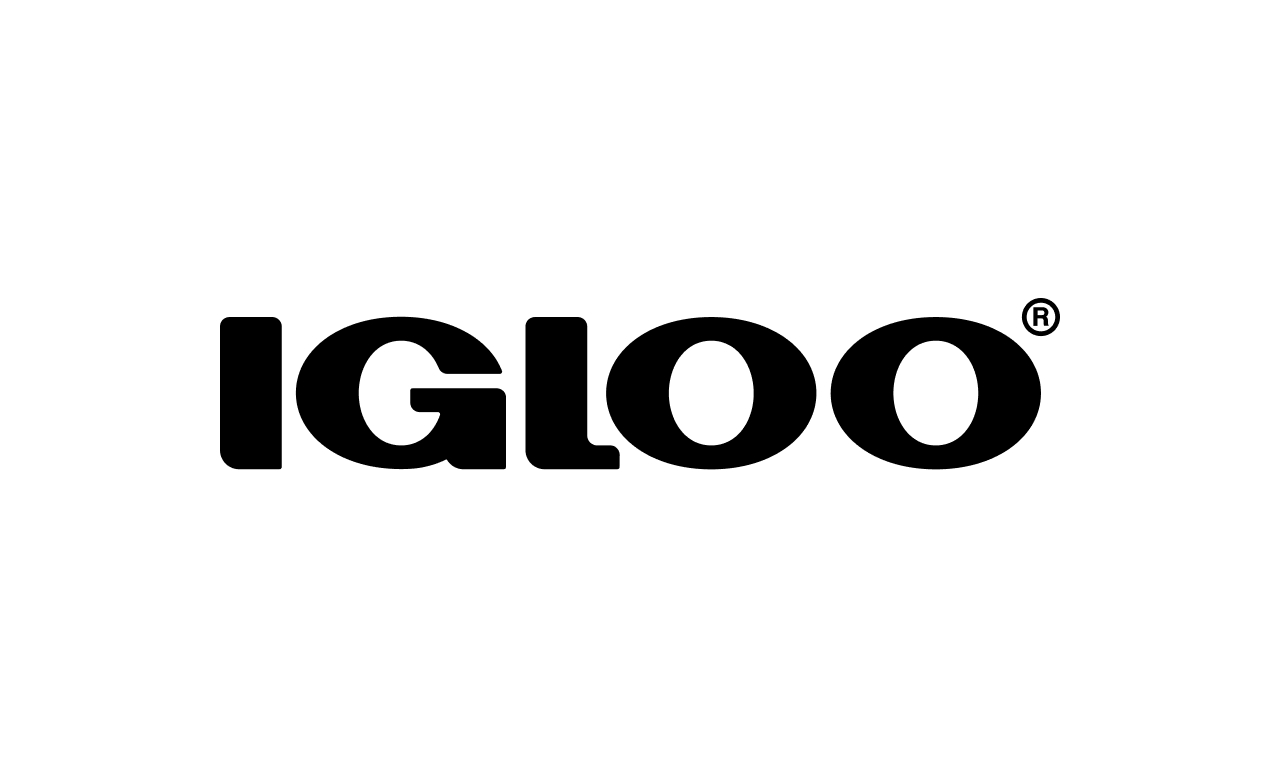
Frequently Asked Questions
Guidewheel gives you a real-time view across every line and site, so you can compare performance, share best practices, and drive improvement consistently across your entire operation.
Guidewheel is designed deliberately to scale quickly. Sensors clip on in minutes, and the system works across machines of any age or type, with minimal IT support required.
Guidewheel doesn’t just show what’s happening, it helps you act. With AI-powered anomaly detection, cross-site benchmarks, and systematized workflows, teams can catch problems earlier, reduce waste, and build on past wins.
Yes. Guidewheel provides accurate, historical data on performance and waste that helps build business cases for equipment upgrades, expansion, or process changes.
Ready to unlock compounding performance gains?
Let’s talk about how Guidewheel helps you scale what works, surface deeper insights, and drive continuous improvement across your operations.