Increase production from your existing assets
Improve the efficiency and output of your factories without adding headcount or equipment.
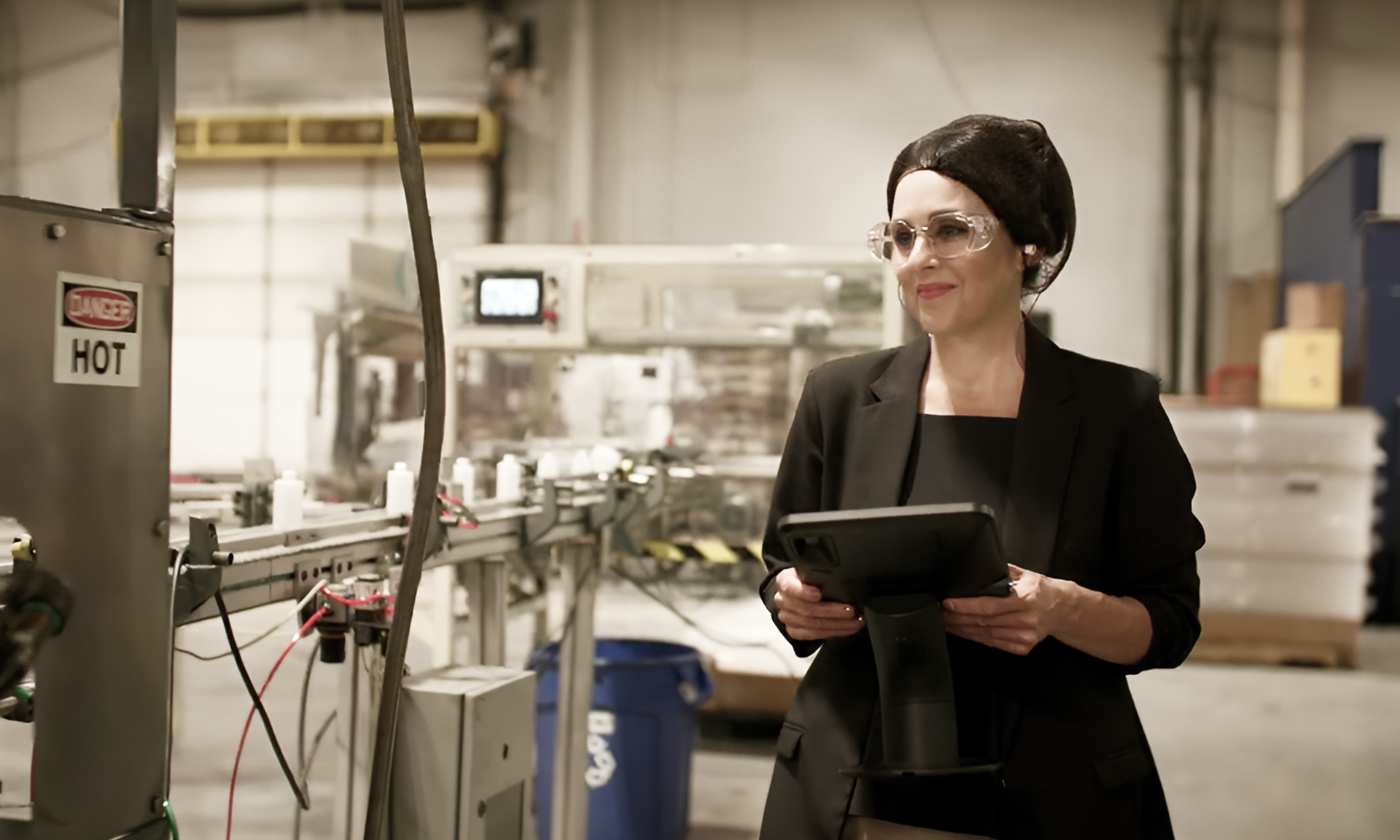
Trusted by hundreds
of leading manufacturers
Stop leaving dollars on the table
In production-constrained environments, capacity is often lost to inefficiencies like late starts, long changeovers, or idle machines, without anyone realizing the impact.
Guidewheel gives your team the visibility to spot and fix these gaps and increase output from your existing resources.
Produce more with the resources you already have
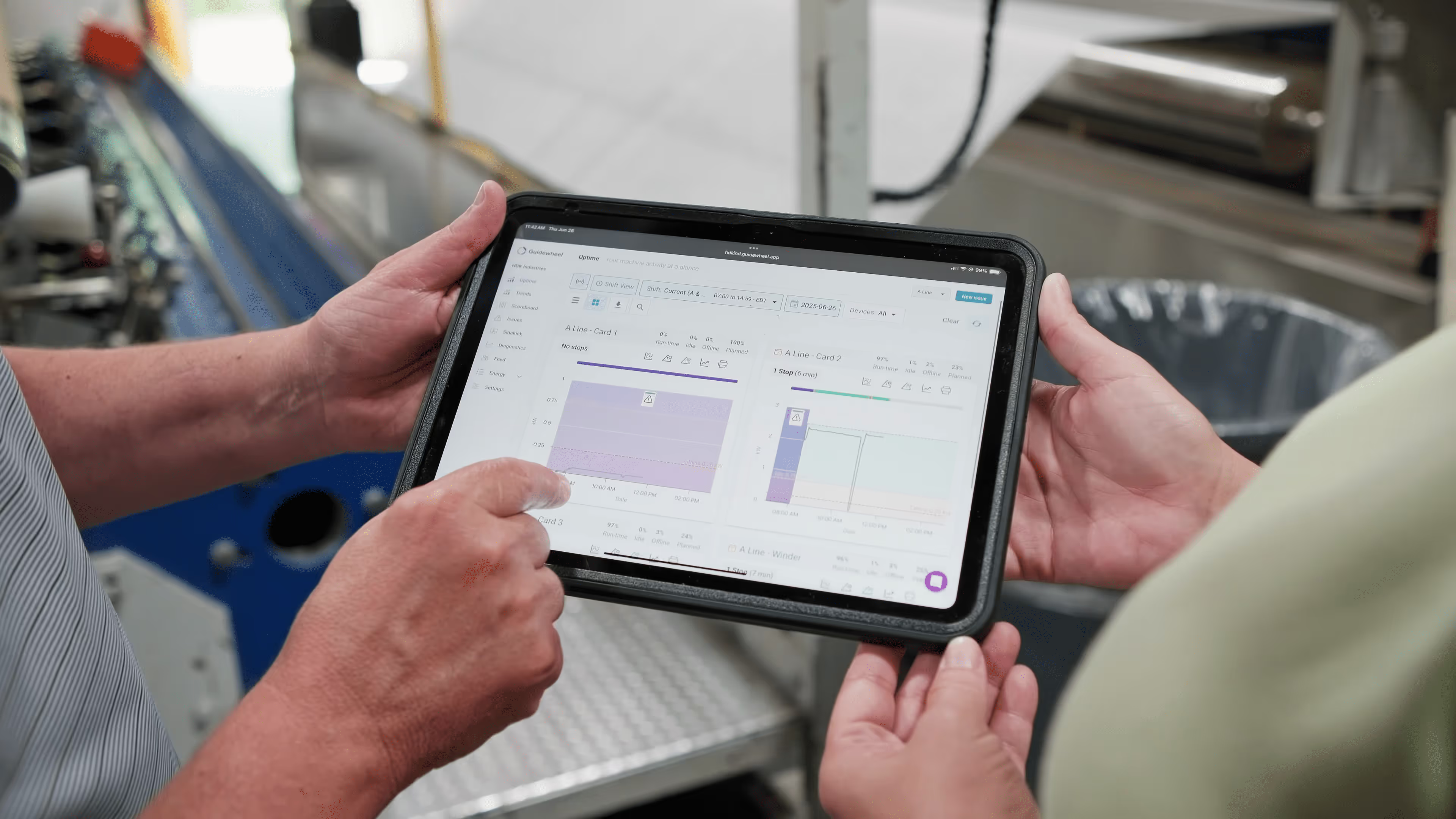
Unlock capacity hidden in everyday delays
Get visibility into slow starts, long changeovers, and inconsistent cycles to recover lost production time and increase output.
Improve cost per unit
Boost machine availability and throughput to get more out of your fixed costs, without adding labor or equipment.
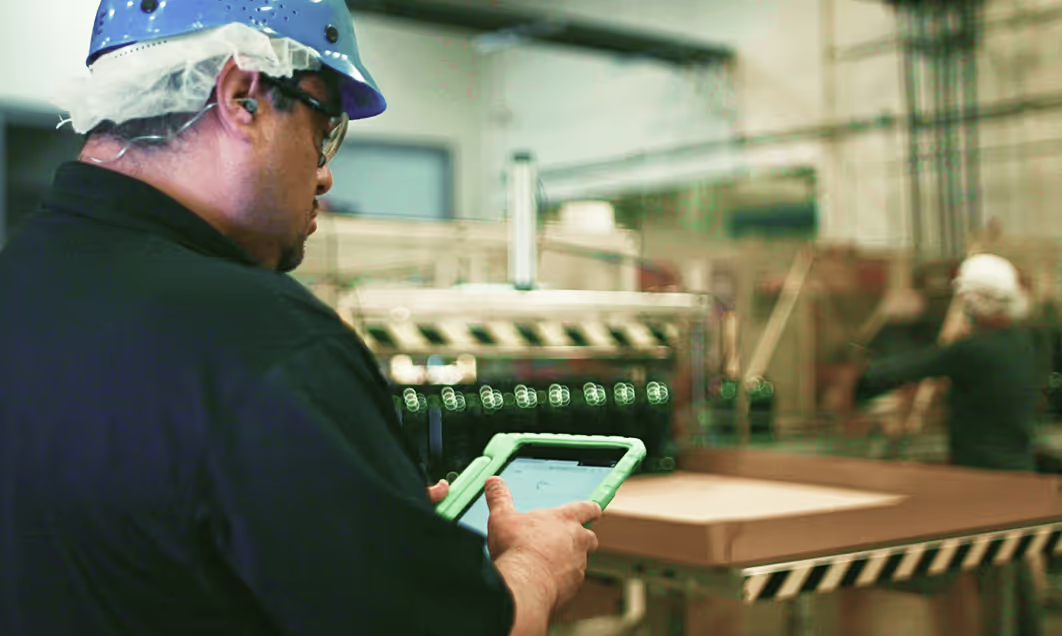
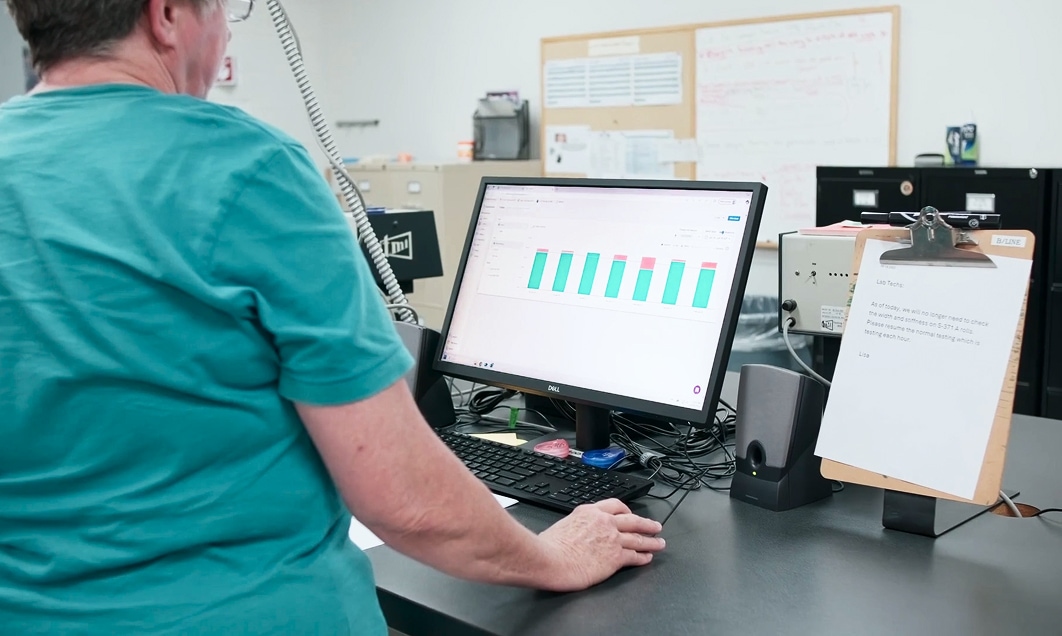
Align teams around performance
Surface production and performance trends by machine and shift so your teams can track progress, stay accountable, and continuously improve.
Lay the foundation for predictive action
Streamline operations and maximize performance with every additional machine, user, and factory added to the platform.
.avif)
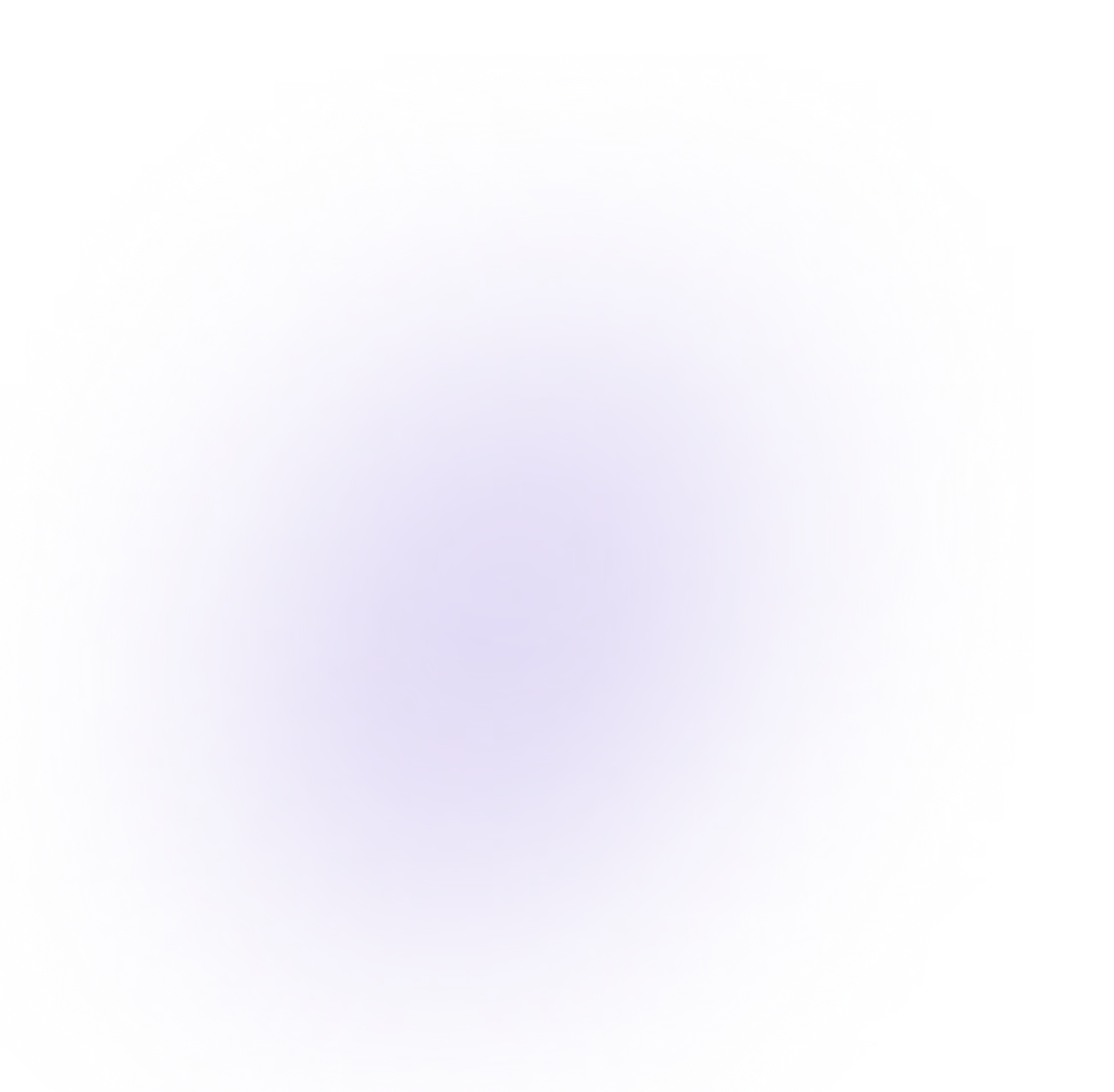
35% increase in utilization at Penn Color
With greater visibility into production bottlenecks and downtime, Penn Color unlocked capacity across their lines, enabling them to take on more business without adding new equipment.
Production & OEE Tracking
Get accurate, real-time production data without manual tracking that’s fully aligned with your team’s workflows and systems.
- Replace manual spreadsheets with automated digital reporting
- Use real-time data to benchmark production performance
- Easily connect data with ERP and other systems for end-to-end visibility
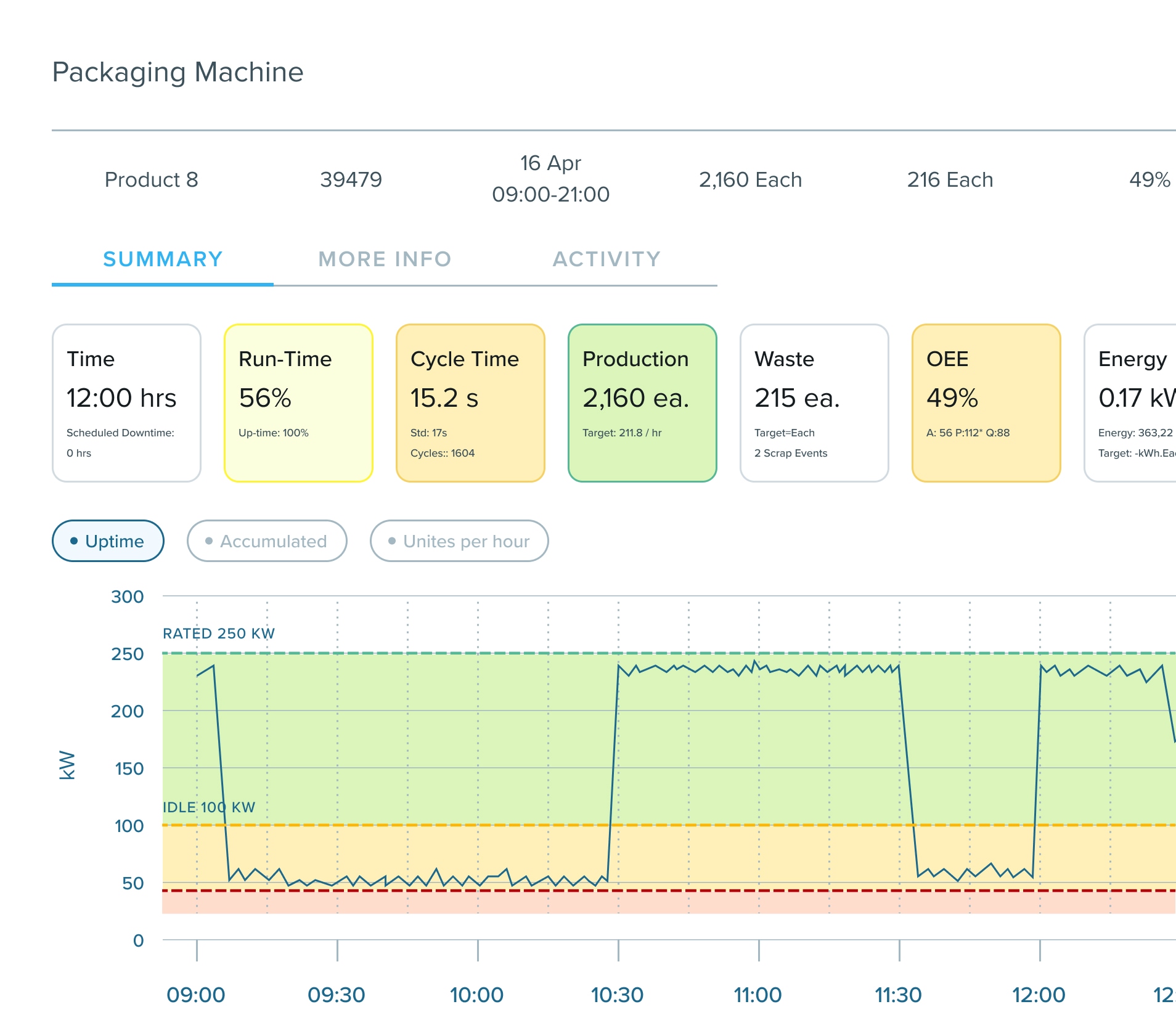
Pareto Analysis
Pinpoint and address your biggest downtime drivers to focus resources where they’ll have the most impact.
- Identify top downtime drivers by machine or type
- See which problems are costing you the most time
- Prioritize improvements based on data, not assumptions
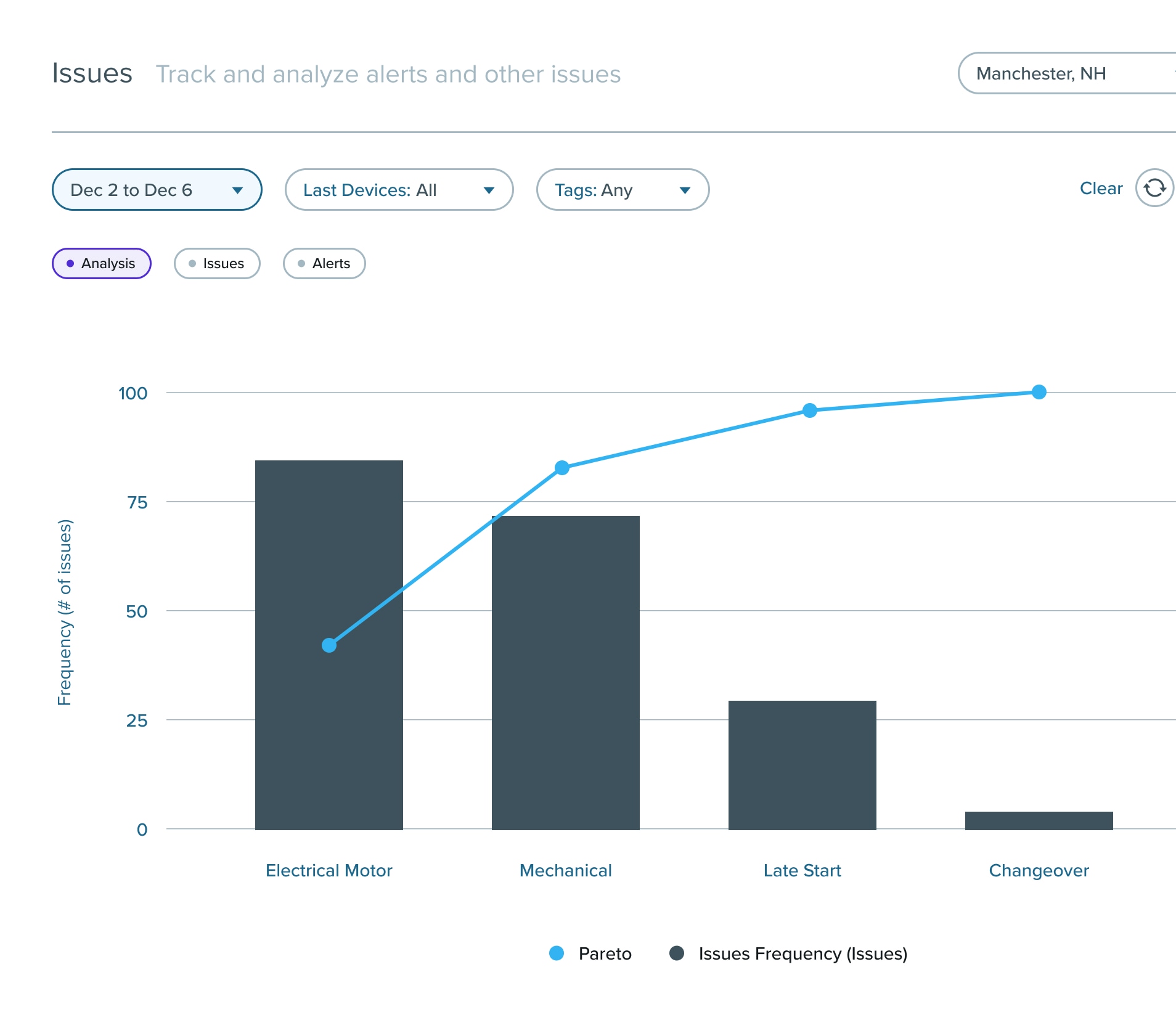
Trends
View how performance is changing over time. Easily spot what’s going well, identify recurring problems, and uncover areas for improvement.
- Prove progress or flag regressions at a glance
- Identify patterns behind recurring issues
- Easily track machine performance over time
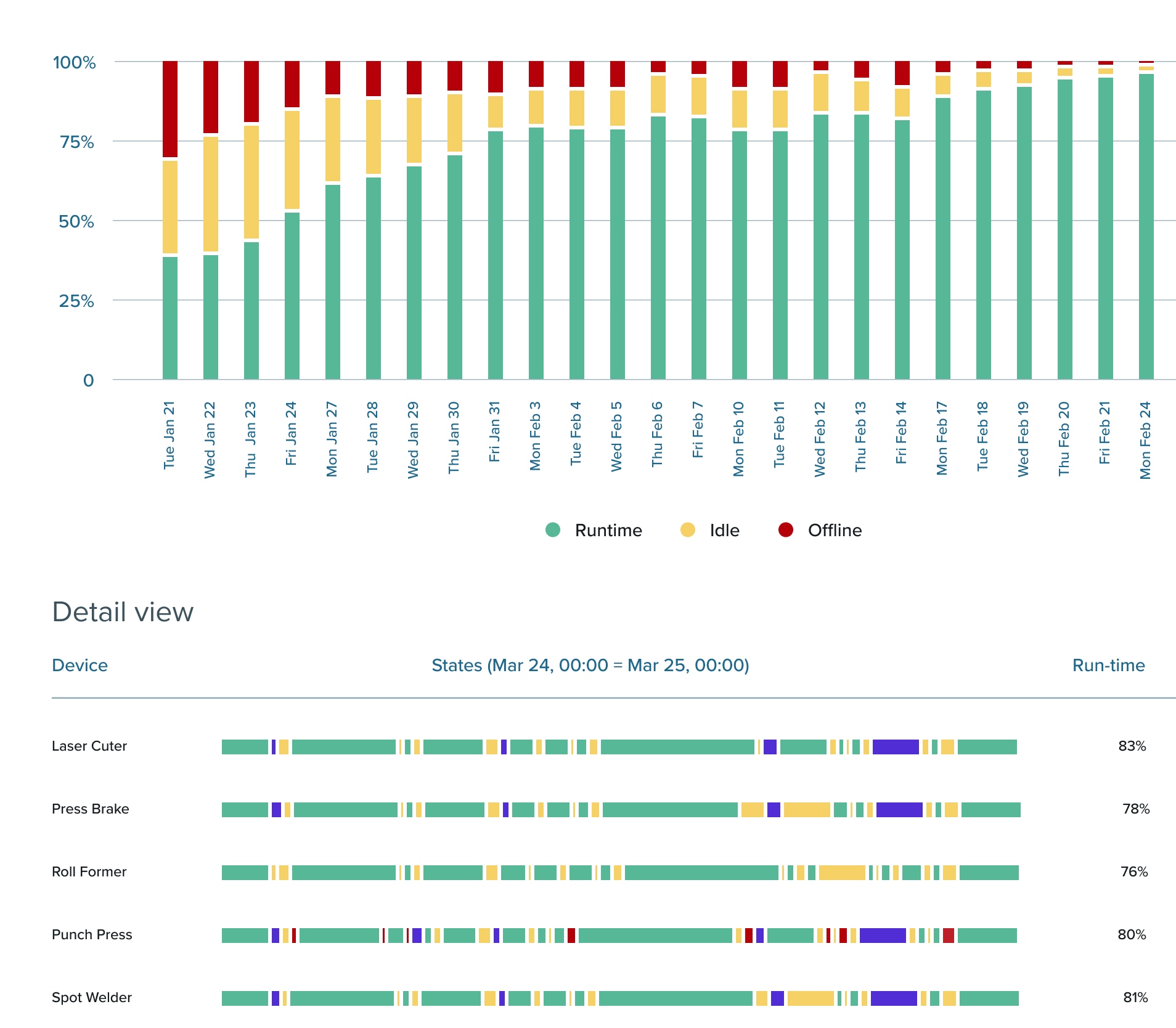
Cycles Tracking
Track cycle times in real time to spot hidden inefficiencies and drive consistent output.
- Easily compare actual cycle times against targets
- Identify where performance drifts from standard
- Uncover bottlenecks and hidden capacity losses
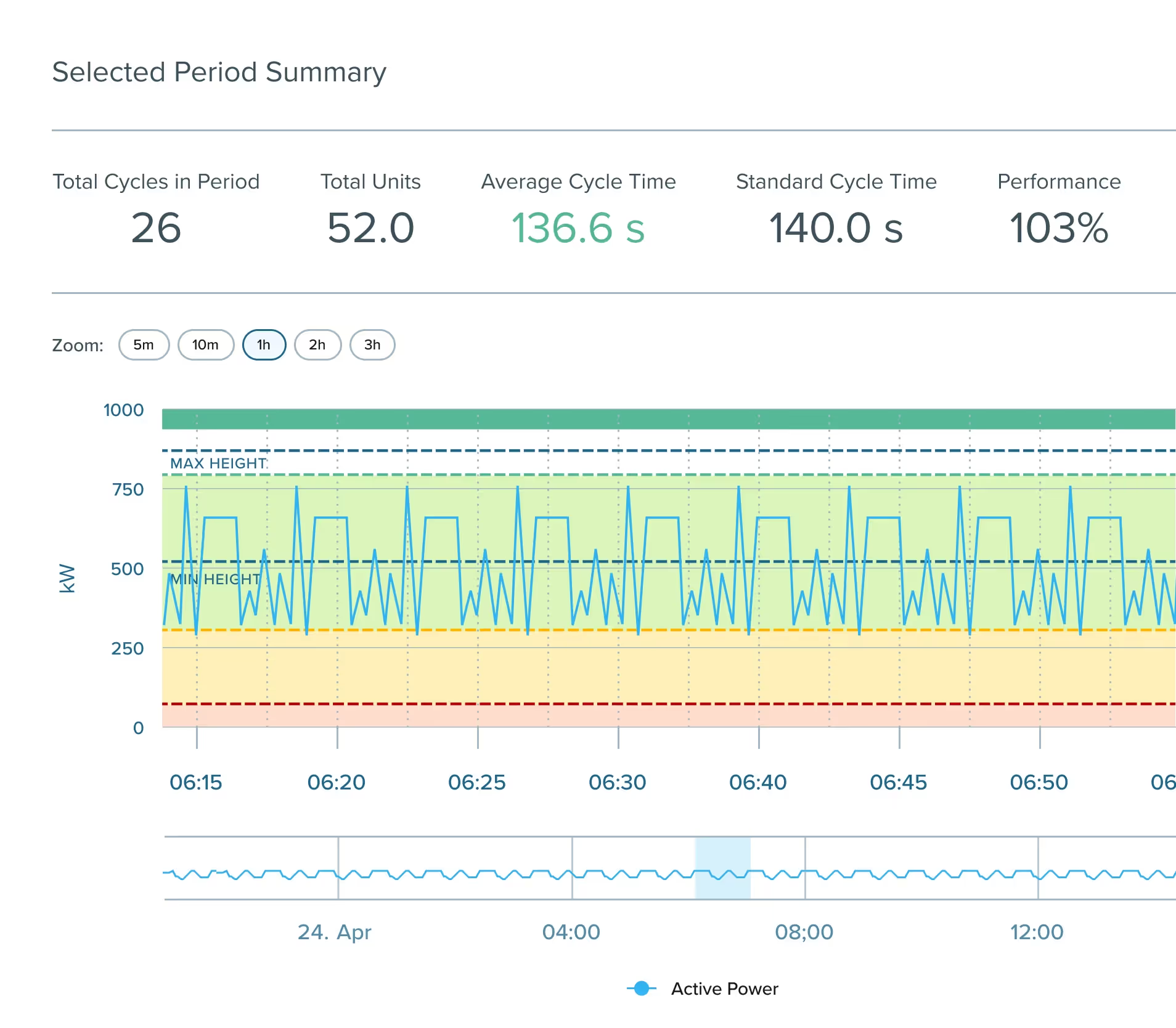
FactoryOps Hub
Bring together the most critical production data in a centralized, real-time dashboard.
- Monitor uptime, OEE, and cycle times in one place
- Compare performance across machines, shifts, or sites
- Align teams with shared, real-time insights
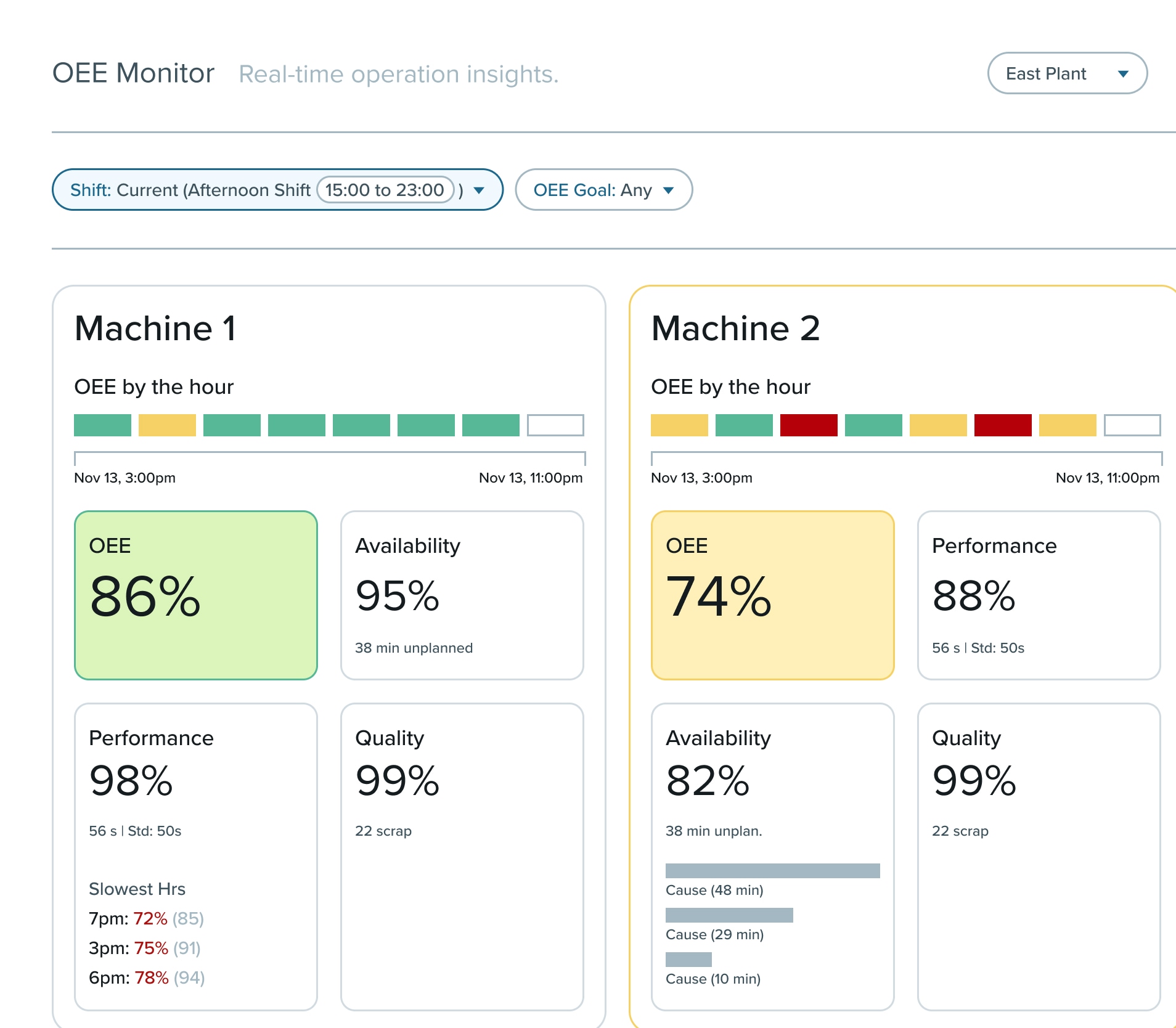
Integrations
Easily connect Guidewheel with the systems you already use to streamline workflows and amplify the value of your data.
- Sync production data with ERP and planning systems
- Trigger maintenance actions through your CMMS
- Feed insights into BI tools and custom dashboards
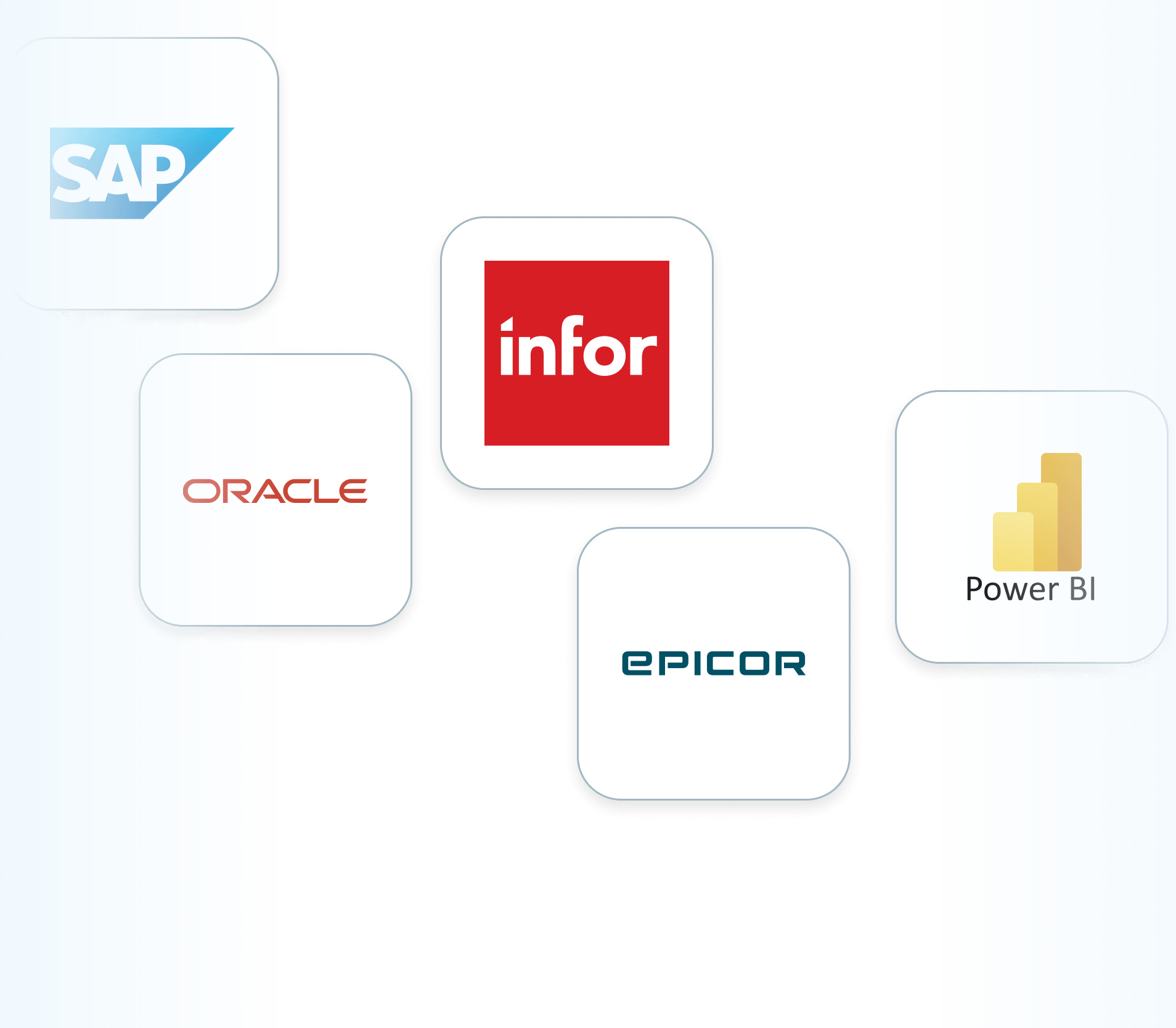
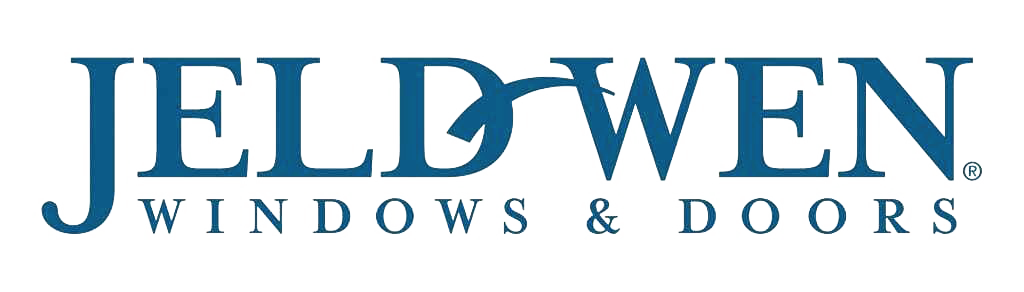
Frequently Asked Questions
Yes. Guidewheel integrates natively with SAP and works seamlessly with other leading ERPs like Oracle, Epicor, Microsoft Dynamics, and more via Workato and our open API.
Guidewheel’s non-intrusive sensor approach means it works on any machine, regardless of age, make, or model.
Unlike traditional systems that are complex, siloed, and require heavy IT support, Guidewheel is lightweight, quick to deploy, and gives you real-time visibility across all equipment without the long set up or high cost.
Most customers are fully up and running within days. Our clip-on sensors and simple setup mean you can start capturing insights and seeing opportunities to increase output quickly.
Ready to increase production from your existing assets?
Let’s talk about how Guidewheel can help you unlock hidden capacity, boost output, and improve cost per unit, without adding headcount or equipment.