Case study
Building momentum with initial wins to reduce downtime by 62%
Updated:
March 9, 2021
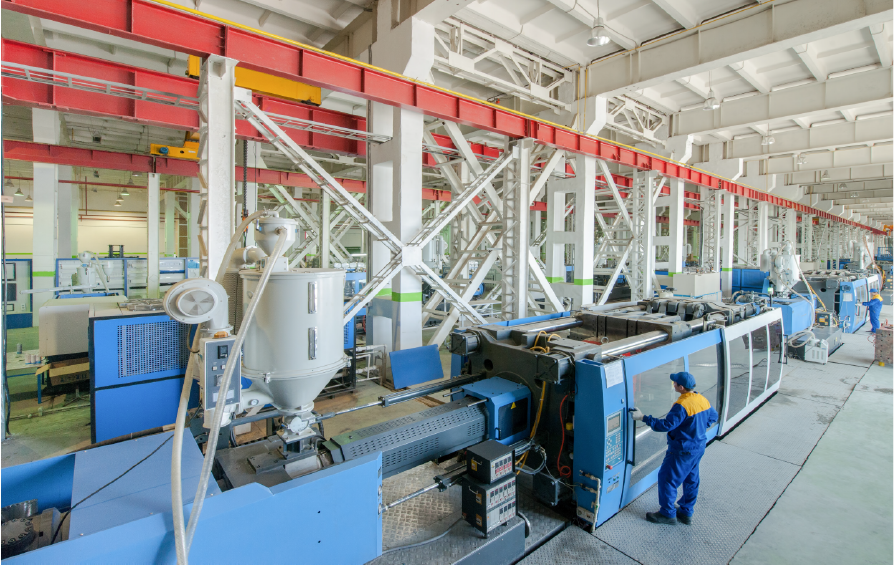
The head of production gritted his teeth as he sent along the day’s downtime summary to the COO. He couldn’t figure out what was causing his machines to be down for so long. At the end of each day, he would collect all the logbooks and tally up the downtime tracked in a massive spreadsheet. But by the time he was able to pull everything together for the COO, several hours had already passed and it was too late to take any action.
He didn’t mind the extra work - frustrating as the spreadsheets were - but he felt the urgency of taking action to get a handle on his downtime. In the challenging economic climate, every minute lost added up into an important cause of loss to the bottom line. He knew every bit of improvement he and his team could make would directly contribute to the company’s ability to stay competitive. So he decided to test out Guidewheel’s real-time platform as a way to bring the team together around shared visibility to reduce lost production time.
The first thing he had to do was get the team on board. At first, he shared a potential goal of reducing downtime across each of his five critical machines. But the team pushed back - reducing downtime in their existing processes seemed completely impossible.
So they decided to start small: On one machine, they would start by reducing lost production time by just five minutes a day.
They established simple but clear processes towards that initial goal. They configured the Guidewheel system to send an alert to the operator and the head of production any time the machine was down for more than their target changeover length. Whenever an alert was sent, the operator needed to provide the reason for the downtime, either through tagging it in Guidewheel or through a text/call to the head of production.
At first, the alerts were ignored. With other texts and calls coming in, it was hard to prioritize the Guidewheel alerts. But then the head of production tried calling the operator as soon as he received the alert to ask the reasons for the downtime. Soon, the team was proactively providing the reasons. Each morning, they could look back at the reasons for downtime, prioritize them, and take action to address the top causes. Even more impressive, their downtime started to decrease.
Soon, the team could see a beautiful decrease in downtime on the first machine they had targeted - effectively reducing average lost production time by 3 hours in a 5-week period! The head of production highlighted the team’s work to the team and the COO, who reinforced the importance of these improvements for the business.
The team was incredibly proud to see the initial results they had achieved together, and was now motivated to achieve more. They decided to expand one additional machine at a time until the same processes were in place across all the key machines in the plant. In under 2 months, they reduced average lost production time for the facility from 4 hours to less than 1.5 hours - a 62% reduction.
The COO has been thrilled with the results and the head of production is gearing up to roll out similar programs at all of their plants. Guidewheel has given him the tools he needs to empower the teams at all the plants to drive improvement - and as a nice bonus, he has also gotten back several hours a day he had previously spent wrestling with spreadsheets!