Unlocking Peak Performance: How Guidewheel Helps Teams Reach Their Goals
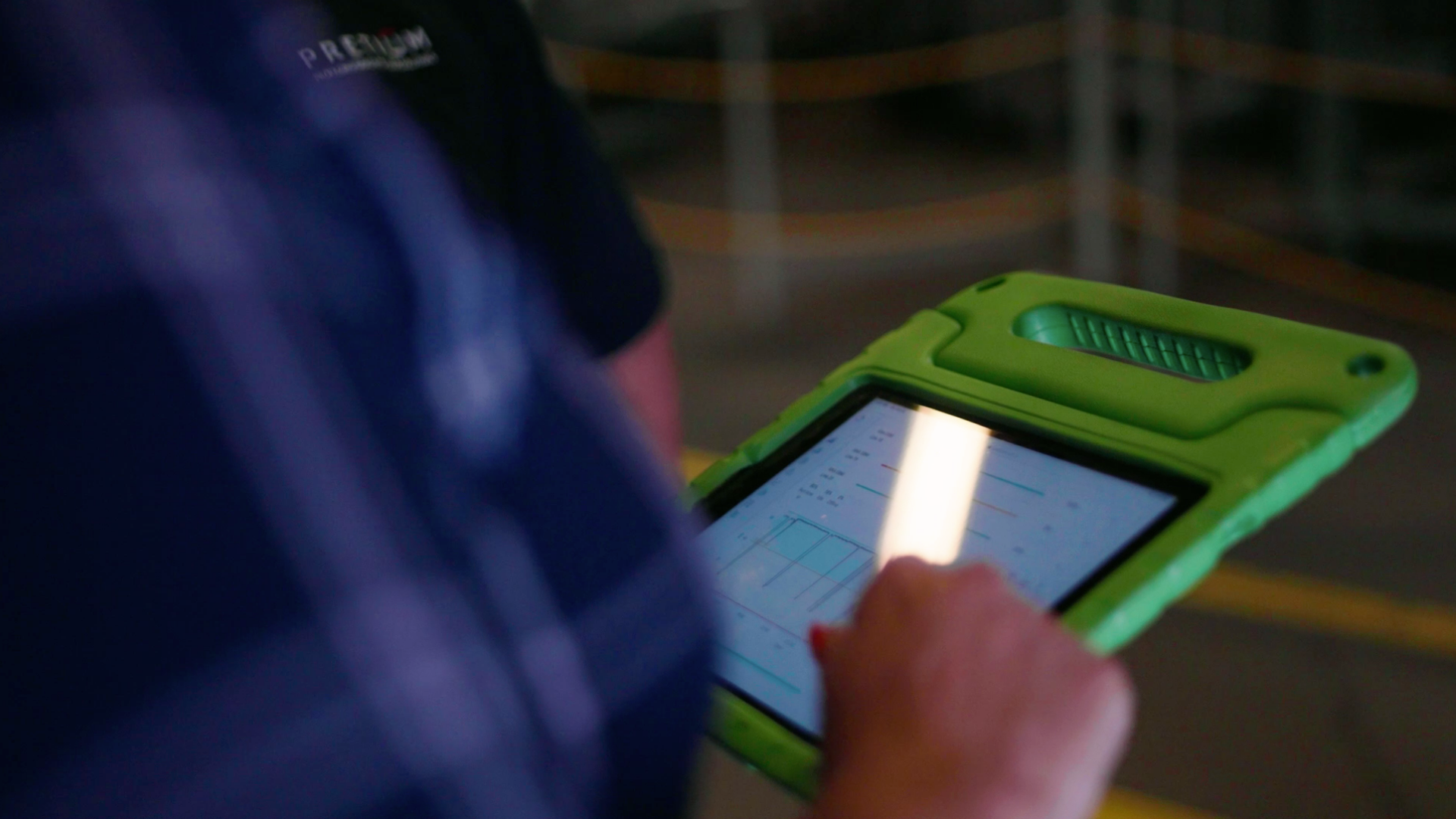
Guidewheel empowers teams to reach peak performance within the three major buckets that make up Overall Equipment Effectiveness (OEE), a gold standard measure of a factory’s productivity:
- Availability: Is equipment running when it should be?
- Performance: Is it running at the right speed?
- Quality: Is it producing good quality output?
For most manufacturers, the biggest returns tend to be found in improving Availability and Performance.
Improving Availability
Improving Availability sounds simple: Decrease unplanned downtime, which will in turn increase parts produced. However, given the many ways downtime from different causes can add up throughout the day, collecting actionable data to inform decision-making and reduce downtime has historically been a challenge. Despite these challenges, managing downtime remains vital to reaching and sustaining peak performance.
Guidewheel helps manufacturers quickly overcome the challenge of tracking downtime by leveraging Current Transformer (CT) sensors that simply clip onto the power source for the main drive or key component of any piece of equipment. These sensors are simple and non-invasive for any team to clip on and get visibility across all their equipment in a single day.
Guidewheel then transforms the second-by-second electrical data streaming from the sensors into key metrics such as runtime, downtime, and cycle time—providing the foundation for visibility and FactoryOps workflows that support any team to control and eliminate unplanned downtime. In this visual, you can see how Guidewheel calculates runtime, idle time, and offline time from an example machine:
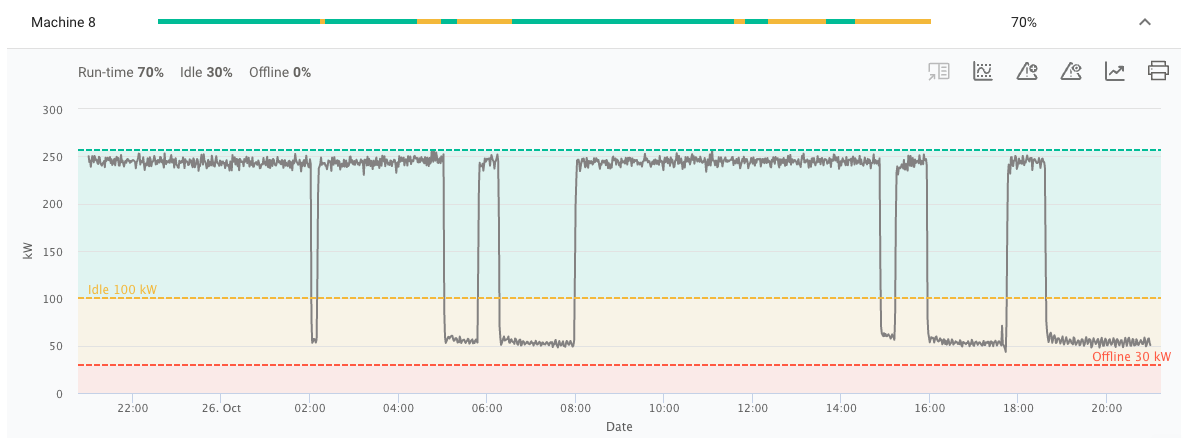
Gaining visibility into machine activity can quickly show areas to improve. The following are all recent examples of insights manufacturers swiftly gained after starting with Guidewheel:
- A third shift responsible for 53% more downtime than the two prior shifts
- Specific operators on the same line consistently producing 14% more than others—with an opportunity to quickly share and spread those best practices across other shifts
- Machines running more slowly towards the end of shifts, delaying changeovers until the next shift and negatively impacting production
- First shifts getting machines running up to 45 minutes after intended start time
Guidewheel then provides all the functionality teams need to continuously improve in reducing downtime:
- Automatic tracking of any incident
- Escalating, configurable alerts so the appropriate teammates can be notified to address problems
- Easy mobile tagging functionality for teammates to add the cause of downtime
- Pareto analysis of top causes of downtime by duration or frequency (see below)
- Automatic calculations of runtime and downtime for any shift or day
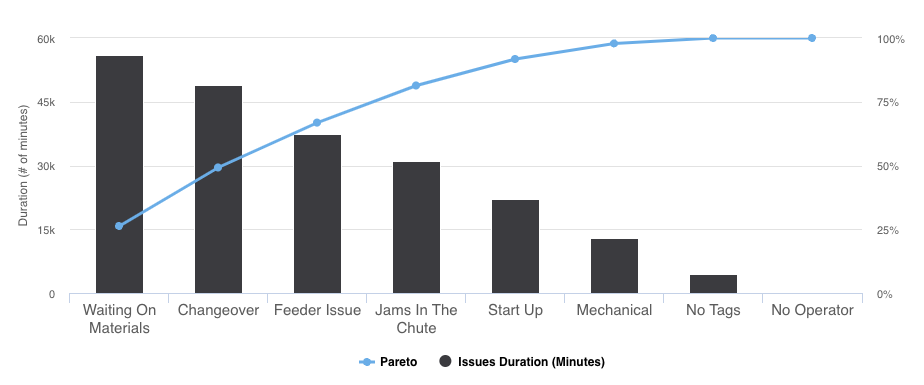
While reasons for downtime vary by customer and with the economy, the top five reasons for unplanned downtime are common at the moment across the hundreds of manufacturers we work with:
- No labor
- Lack of materials
- No work for the machine
- Maintenance
- Changeover
For these downtime reasons and others—the system is configurable to track and manage the downtime reasons most meaningful for your company—Guidewheel provides your team with the data and support to gain actionable insights to improve.
We make these insights easy and functional through customizable alerts (to react faster, when it happens) and automated analytics (to help you know where to focus long-term improvement efforts).
Improving Performance and Quality
Guidewheel also supports teams in improving the second bucket of OEE: Performance, the rate at which product is produced. With the same plug-and-play sensor approach, Guidewheel tracks the cycle time and provides reporting and insights to help teams understand how they are performing in relation to their production goals.
First, Guidewheel’s software tracks the unique signature of each cycle on discrete processes to accurately calculate and report on cycle times and cycle counts. This automation of cycle time data collection enables teams to gain a better understanding of their process.
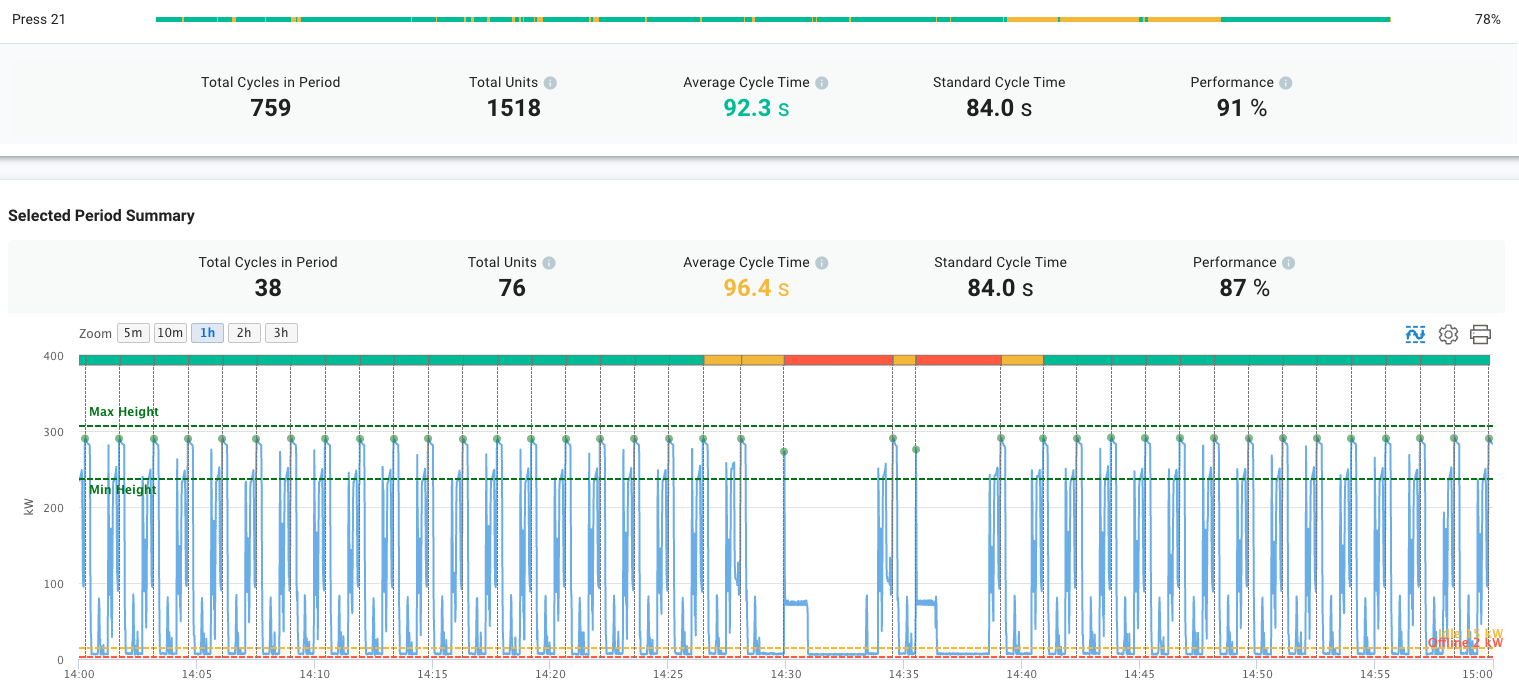
Additionally, Guidewheel can flag off-standard cycles that can be an indicator of quality or maintenance issues. The system can be configured so that an increase in the electrical draw, often associated with maintenance issues, sends out an alert to a relevant member of the team, or so that an off-standard cycle is flagged and color-coded for the team to take action.
Through focusing on improving Availability and Performance, customers have achieved incredible results. In addition, the last component of OEE, Quality, can currently be tracked in Guidewheel through inputs from your production data or using Guidewheel’s open API to automatically pull data from the ERP or other systems—and customers also use many aspects of Guidewheel’s alerting and visibility functionality to help improve Quality (detailed example here).
Other Benefits
Guidewheel also brings benefits to manufacturers beyond improving OEE. The flexibility and versatility of the CT sensors Guidewheel starts with makes it easy to clip on and monitor the process of any machine with the same level of data accuracy and insight—which means that many teams get a lot of value from clipping in auxiliary equipment and production infrastructure in addition to core production machines.
Recent specific examples of these types of additional value include:
- Preventing up to 10 hours of unplanned downtime for a full facility by immediately detecting and alerting the team to a problem with a cooling tower pump
- Identifying critical air compressor leak that previously went unnoticed
- Being able to accurately track energy use across all types of equipment, identifying high-ROI opportunities for process or CapEx improvements
- Identifying that just 1% of machines accounted for 23% of total idle time energy consumption—flagging opportunities to quickly achieve significant savings in energy costs
- Being able to track and get alerted to peak facility electrical consumption to avoid peak penalties
Reaching and Sustaining Peak Performance
We all know that data is only as valuable as the decisions it informs and actions it inspires. Guidewheel was built with that in mind – to equip teams with the tools they need to make the best decisions to improve their business.
Regardless of industry, process, or revenue, Guidewheel’s approach will likely provide you with insights that can help immediately improve operations across the board. If peak performance, increasing OEE, or simply getting better is a goal of yours, consider using Guidewheel to get you there faster.