Case study
RAPAC uses Guidewheel to reduce scrap and improve quality
Updated:
July 26, 2022
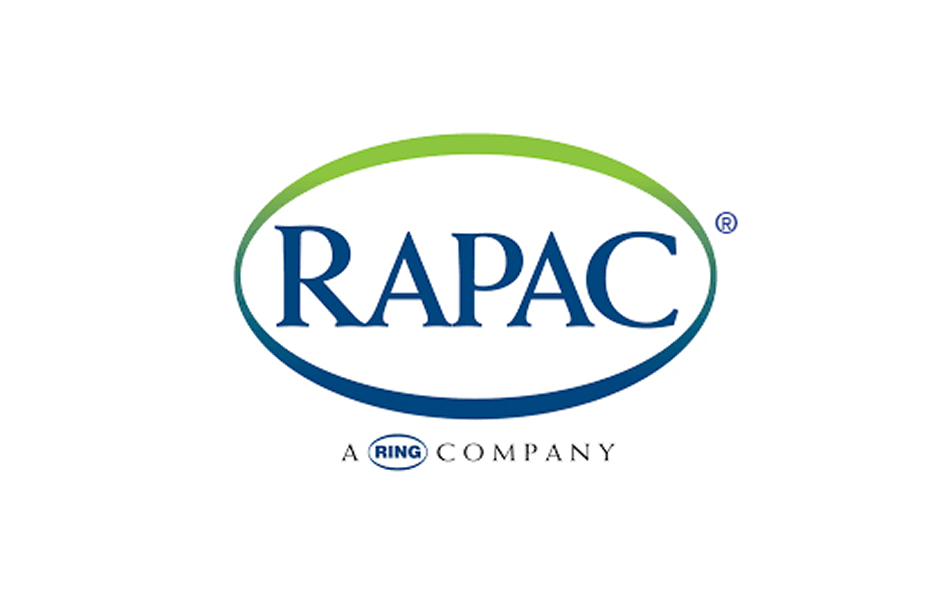
RAPAC, headquartered in Oakland, Tennessee, is the one of the largest EPS recycling and services companies in the world. As an industry leader in the use of recycled content, RAPAC offers applications of polystyrene including both EPS and PS products, as well as proprietary, custom resins for a multitude of industries and applications.
Steven Cummings, Maintenance Manager at RAPAC spoke with the Guidewheel team in July to share how he and his team are benefiting from using Guidewheel to not only measure machine runtime, but to reduce scrap and improve quality in addition to improving production efficiency overall.
“Guidewheel has been fantastic for RAPAC. So great! We never had this in the past. We've always tracked through human interaction and writing on pieces of paper. Guidewheel has been a game changer to actually capture uptime and downtime, and for us to capture top losses.”
Here, we share details on one of the ways RAPAC uses Guidewheel: as a leading indicator to reduce scrap and improve quality.
The problem:
Minimizing scrap is an important concern for many industries. Many manufacturers are looking to reduce waste of raw material — which can be expensive and hard to access reliably given recent supply chain challenges— to keep COGS low. Others want to prevent any chance of out-of-spec products making their way to customers, damaging those relationships or requiring replacement at massive expense.
Regardless of the motivation to reduce scrap, the best way to ensure high quality is by catching the problem quickly and at the earliest stage possible in the manufacturing process. In these examples, we share some ways manufacturers are leveraging Guidewheel’s FactoryOps platform to catch issues early and address these problems with leading rather than lagging indicators.
Example 1:
Manufacturers such as RAPAC, who have machines that need to run within very specific parameters and have important requirements for material quality and quantity, can use Guidewheel’s visibility and alerts to identify leading indicators for quality problems.
“Guidewheel is a leading indicator for us to discover potential quality issues.”—Steven Cummings
In this screenshot, for example, you can see an example of an extruder experiencing a problem. When the load drops into a yellow zone, the drop is usually a leading indicator for a potential problem. They call these drops “yellow flags” that indicate something is different in the material being dumped into the machine—and they need to take action to get it back up into the green.
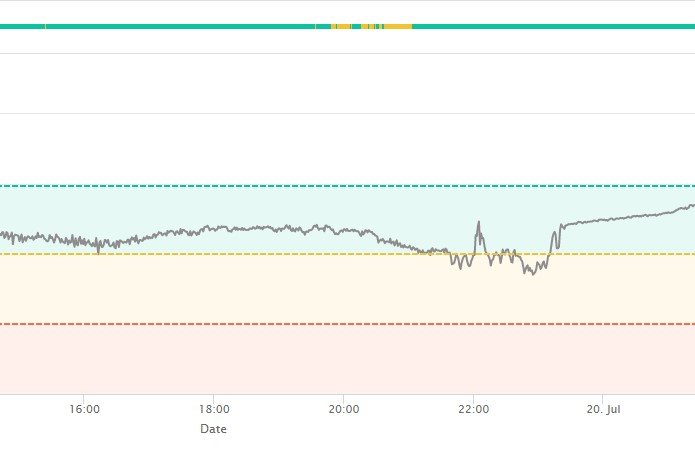
In this case, the team saw the pattern change, investigated the “yellow flag,” and learned it was a material quality issue. One of the mixers had failed and dumped an incorrect amount of one type of material into the extruder, which reduced the load. Using Guidewheel, they were able to immediately catch the problem and address it.
Similarly the second screenshot below shows what Steven saw when he was checking Guidewheel one Sunday. He saw a particular line experienced some downtime, then came back up—but to yellow rather than the usual “green, all good” state. He could see from the data in Guidewheel that something was clearly wrong. Steven and the team pulled the extruder screw and found material in the screw that was preventing it from getting a good bite.
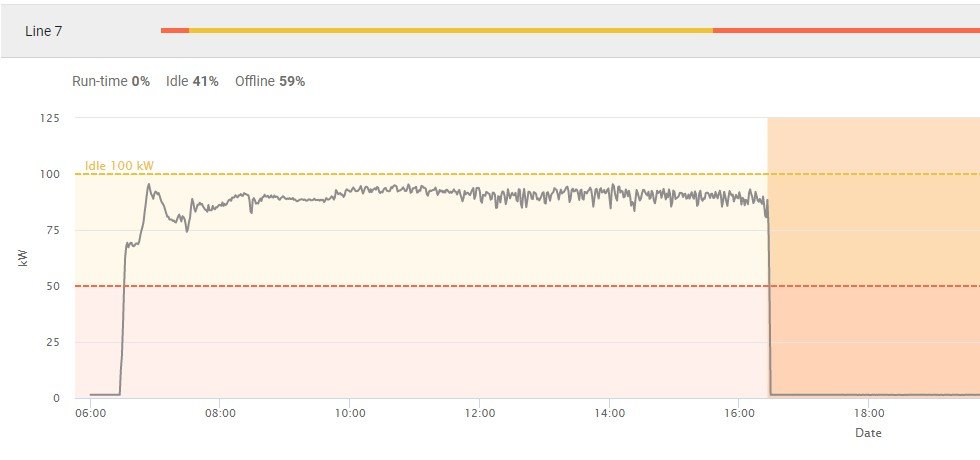
He describes, “Guidewheel showed something was happening that we never would have seen prior to Guidewheel. Because of being able to see the issue, our response time was much faster. We pulled the screw much sooner whereas normally we wouldn’t have seen it and would have run with the problem for more than a week.”
Since catching potential quality problems quickly is so critical for the team, Steven has set up monitors in the plant to constantly refresh Guidewheel so that in addition to getting the alerts, they can immediately see the problem visually: “I’ve got it on a screen. My team’s eyes are always on that, and I’ve got alerts set for all the potential issues.”
Example 2:
Quality problems can also stem from problems with support equipment such as compressors, dryers, and chillers. These issues can be particularly problematic as they may be more likely to go unobserved at first than problems with core production equipment. For example, one manufacturer describes the terrible problems they experienced when their primary air compressor and secondary air compressor both went down — and no one on the team realized!
The plant team reacted swiftly to prevent any such incident in the future by clipping Guidewheel on to their air compressors. Now, they can get alerts right away any time the primary compressor goes down so they know they’re running on the secondary compressor—and can escalate immediately if they get an alert that the second compressor is down as well:
Steven describes the way he likes these alerts to escalate from Guidewheel: “For compressors, I’ll have it text me or my team alerts because that’s critical. Any time our primary compressor goes down, I need to know about it.”
These represent just a few of the ways Guidewheel can be used to improve quality and reduce scrap on the plant floor — in addition to improving production efficiency— to further improve business results.
Our thanks to the Guidewheel customers who share the examples highlighted here. If you and your team would like to showcase how you are using Guidewheel to drive business results—or don’t yet use Guidewheel, but would like to!—send us a note at info@guidewheel.com.