Manufacturing Optimization: Enhancing Efficiency and Productivity
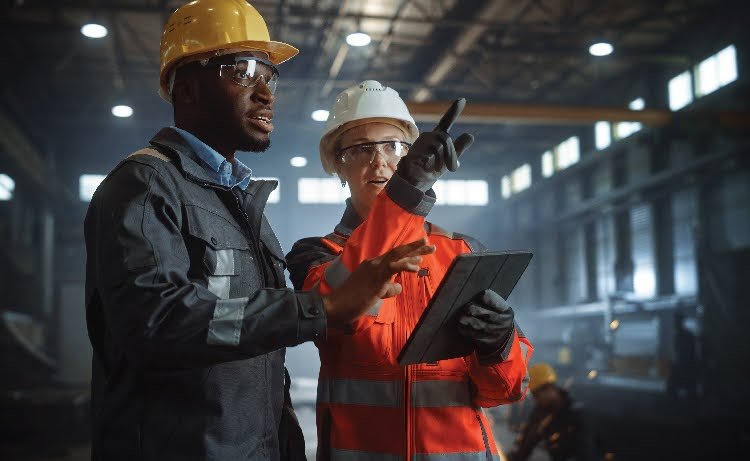
Table of Contents
- What is Process Optimization in Manufacturing?
- Components of Process Optimization in Manufacturing
- Benefits of Manufacturing Process Optimization
- Challenges in Optimizing Production Processes
- Optimizing Production Processes with Data
- Unlock Your Manufacturing Optimization Potential with Guidewheel
Production excellence starts with alignment between machines, processes, and people. When teams see what’s working and where to improve, they make faster, smarter decisions.
Real-time data transforms this approach from reactive to proactive. When floor personnel see precisely what's happening in production, they address issues before escalation and make decisions based on facts rather than assumptions.
This article shows how systematic process optimization drives results through targeted improvements, not major overhauls. The sections below outline strategies for turning data into action and delivering measurable gains with minimal investment.
What is Process Optimization in Manufacturing?
Every production process contains hidden opportunities. Optimization uncovers these possibilities through systematic analysis and targeted action. This approach removes bottlenecks, reduces downtime, and improves flow between production steps.
Rather than reinventing operations, effective optimization builds on an existing foundation. When applied consistently and based on real performance data, small changes create compounding benefits that amplify throughout the production chain.
Production process optimization, meaning improving production at a functional level, connects insight with execution. When production data flows freely between systems and people, performance improves without adding unnecessary complexity.
Components of Process Optimization in Manufacturing
Production optimization relies on a set of core elements that work together. Each one improves a specific part of the process—speed, accuracy, consistency, or visibility.
When teams focus on these components, they build a stronger operation. The goal is to increase output, reduce waste, and make better use of existing resources.
The sections below break down the most effective strategies and show how they support better performance across the factory floor.
Process Analysis
Every improvement starts with visibility. Before teams can act, they need a clear picture of how production moves from one step to the next.
Begin by gathering direct data from the floor. Focus on cycle time and resource use. Then, map the process as it happens, not as it's supposed to work. Bottlenecks appear faster when teams look at actual flow rather than assumed structure.
Use structured root cause analysis to dig deeper. This systematic approach helps expose the source of recurring slowdowns or defects and understand what triggers them.
Once issues are identified, define specific performance measures. These indicators allow teams to track whether a fix delivers the intended result or needs refinement.
Lean Manufacturing
Lean manufacturing focuses on maximizing value while eliminating waste throughout production. Manufacturing leaders apply these principles to produce exactly what customers need using minimal resources. This approach reduces inventory costs, shortens production cycles, and improves quality by spotting defects earlier. Every change aims to remove friction from the process.
A key focus of lean is reducing the eight common types of manufacturing waste. These losses build slowly but drain efficiency if left unaddressed, threatening factory optimization.
Visual management tools help teams see how materials and information flow through production. When bottlenecks appear, standardized processes make identifying the root cause and implementing fixes easier.
Lean adapts to each plant, line, and team. Small, frequent improvements paired with tools that empower action make the biggest impact.
Technology Integration
Technology plays a critical role in process optimization when introduced with purpose. The goal isn’t to digitize for the sake of modernizing—it’s to remove guesswork, speed up feedback loops, and support stronger decisions on the floor.
Automated data capture is a key part of this. When teams no longer rely on manual inputs, they spend less time collecting information and more time acting on it. That shift opens the door to better planning, fewer errors, and faster response to unplanned events.
Predictive maintenance tools extend that value. With machine monitoring software tracking real-time conditions, teams can act early and avoid costly disruptions. These insights also reveal longer-term patterns that lead to smarter resource allocation.
Effective tech integration starts with alignment. Clear ownership, proper training, and early wins all optimize the manufacturing process.
Six Sigma
Six Sigma provides manufacturers with a proven structure for reducing defects and building consistency across operations. Its five-phase approach—Define, Measure, Analyze, Improve, and Control—guides teams through identifying and correcting issues that impact performance.
It starts by defining the issue and setting a goal. Next, teams measure current performance and analyze that data to find the source of variation. Improvements are then tested in real conditions. The final step locks in gains by putting controls in place.
This method is especially effective when applied to recurring issues that resist quick fixes. It creates accountability at every stage and helps teams progress with evidence-based changes.
Enhancing Collaboration and Communication
Manufacturing optimization depends on clear communication channels between departments. When production, maintenance, and management teams share the same data and insights, decisions happen faster and with greater alignment. This responsiveness becomes a competitive advantage in adapting to market demands.
Continuous Improvement
Continuous improvement transforms optimization from a project into a permanent mindset. Instead of waiting for large initiatives, build small refinements into daily operations.
This relies on the fundamentals established in previous steps: process visibility, waste reduction, and technology-enabled insights. Operations personnel use real-time performance data harvested from production monitoring software to identify specific areas for adjustment, implement targeted change, and then measure its impact on overall results.
Over time, these steady refinements strengthen productivity and allow for faster adaptation to changing market demands—a natural evolution of the Six Sigma and lean principles discussed earlier.
Benefits of Manufacturing Process Optimization
Manufacturing process optimization strengthens how operations run, making good factories great. More transparent processes create predictable production cycles and better resource utilization, helping plants confidently meet customer expectations.
Increased Productivity
Strategic changes like minimizing setup time or improving workstation layout reduce idle time and accelerate production cycles. Even small shifts in workflow design can add minutes back to every run.
With shorter cycles, factories can handle more orders in the same timeframe, boosting throughput without extra labor or overtime. These capacity gains help meet demand faster and keep margins intact.
Cost Reduction
Eliminating waste in time, materials, and energy trims costs across the board. Simplified handoffs, leaner inventory, and less rework contribute to more substantial margins. These gains also create breathing room. Whether reinvested in equipment or passed to customers through better pricing, every saved dollar strengthens long-term flexibility.
Improved Quality
Standardized processes deliver consistent results. When each step is clearly defined and closely monitored, product variation drops, and so does the need for inspection or rework. Quality builds trust. Fewer defects mean lower returns, stronger customer relationships, and more room to lead on performance, not just price.
Enhanced Flexibility
A production line that can switch between SKUs with minimal changeover time is more responsive to shifts in demand. Plants that standardize material handling across workstations can shift labor between lines with less delay. These capabilities are often the result of earlier optimization work—simplified workflows, shared data access, and reduced reliance on manual inputs.
Challenges in Optimizing Production Processes
Optimization introduces change, and change takes coordination. Teams may hesitate to adjust routines, especially when those routines feel familiar. Bringing people into the process early, showing results clearly, and sharing ownership often turns hesitation into buy-in.
Investments in tools, training, or systems can also raise questions. However, the value becomes clearer when data becomes easier to access and processes become easier to adjust. The same tools that improve efficiency also build flexibility, setting the foundation for stronger decisions and faster progress.
Optimizing Production Processes with Data
Different types of analytics help you operate more efficiently by turning raw data into actionable insights. Here's how each type can improve your manufacturing process:
Real-Time Data Analytics
Real-time analytics provide immediate visibility into production activity. As machines run, live data shows what’s performing as expected and where performance starts to shift. With downtime tracking software, teams can spot unplanned stops the moment they occur and investigate the cause without delay.
This level of visibility supports faster decisions. A sudden drop in cycle time, an unexpected stop, or a shift in equipment load becomes actionable within minutes. With fewer delays in detection, teams reduce unplanned downtime and keep production moving with greater confidence.
Descriptive Analytics
Descriptive analytics help teams understand how production has performed over time. Reviewing trends over time helps surface recurring issues, slowdowns tied to specific shifts, or performance gaps across similar lines. This creates a reliable baseline. With a clearer view of what’s typical and what’s not, teams can set smarter benchmarks and trace which changes delivered the strongest results.
Predictive Analytics
Predictive analytics flag early signs of performance drift. When data trends point toward equipment fatigue or slowing output, teams can intervene before a failure stops production.
Tools like equipment maintenance software support this effort by making those trends visible in real time. With better timing around service schedules, operations avoid last-minute disruptions and protect uptime across shifts.
Prescriptive Analytics
Prescriptive analytics take insights further by recommending specific actions based on current and historical data. Instead of flagging a slowdown, the system might suggest reordering steps in a workflow or adjusting staffing levels to keep production balanced.
Supply Chain Analytics
Supply chain analytics map the connection between inbound materials and production flow. They help uncover whether supplier delays, transport variability, or inventory gaps are slowing the floor. Once those relationships are visible, operations planning becomes easier.
Quality Control Analytics
Quality control analytics monitor production conditions as they happen. A change in temperature, pressure, or speed can trigger early warnings that something’s moving out of spec.
These signals help teams correct issues before they create defects. Over time, they also highlight longer-term trends that point to where process stability can be strengthened without adding complexity.
Unlock Your Manufacturing Optimization Potential with Guidewheel
At Guidewheel, our FactoryOps platform turns machine-level power data into clear, immediate insight. Our clip-on sensors connect to any machine, old or new, without changing your infrastructure or interrupting production. Within hours, your team gains real-time visibility into runtime, downtime, and performance across the entire floor.
That visibility is just the first step. Our AI-powered system constantly analyzes those signals to surface trends, flag anomalies, and recommend targeted actions that reduce waste, improve OEE, and prevent costly delays. Teams get the information they need when they need it in a format that supports fast decisions.
With a platform built for scale, operations leaders can track metrics across multiple plants, standardize reporting, and replicate improvements line to line. From reducing idle time to extending asset life, Guidewheel makes it easier to improve outcomes without overhauling your systems.
Start optimizing with the machines you already have. Contact us today to learn how we help you make every minute of production count.