Case study
Pretium optimizes production and lowers energy consumption across 25+ locations
Updated:
September 27, 2023
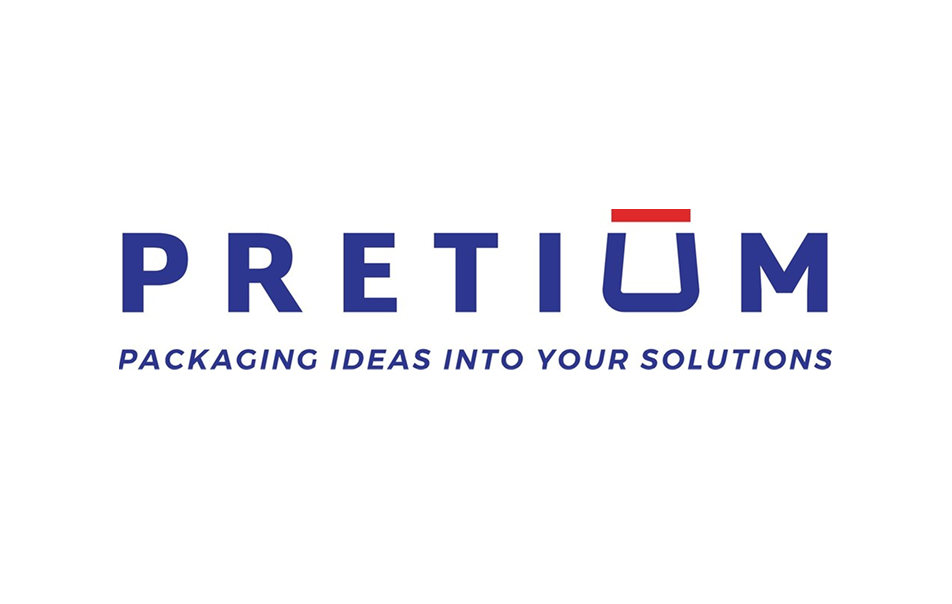
Pretium Packaging is a manufacturer of rigid packaging solutions for specialized applications with small to mid-sized production volumes. Pretium started with Guidewheel in November 2020 and now uses Guidewheel across all of their 26 facilities in 5 countries worldwide.
As a quickly growing organization that regularly makes acquisitions, Pretium was looking for a way to get operational visibility across all their factory locations under one umbrella. Overall operational visibility into key metrics such as machine runtime and production would be key to driving efficiency, and driving both growth and margin improvement over the short and long term. In addition, they wanted a way to reduce energy costs, not only as an important financial driver but also as a key to improving the sustainability of their operations.
"You can’t manage what you don’t measure. GHG emissions and energy usage were never more measurable and in real time than with Guidewheel. If you are serious about improving efficiency and reducing emissions you need to consider Guidewheel,” said Paul Kayser, CEO of Pretium Packaging, which uses Guidewheel across all of their 25+ plants globally.
Pretium views increasing production efficiency by lowering energy consumption as a win/win for both business profitability and emissions: Every minute their machines are not running efficiently (hurting production) is a minute lost of good production and a minute they are wasting energy (hurting emissions).
They were committed to achieving those win/wins to increase sustainability in their operations, but before using Guidewheel, lacked granular data to understand what specific process improvements they could be making. They frequently had visibility into the overall energy consumption of the site, but lacked visibility into energy efficiency of individual machines and ancillary equipment.
To solve this problem, Pretium identified Guidewheel’s FactoryOps platform as the fastest and most cost-effective solution. Guidewheel allowed them to swiftly connect all of their equipment and factories in one platform to manage both operations and energy. Guidewheel’s design made it straightforward for any of their factory teams to clip sensors on their machines and get visibility within days or weeks. Now 18 months later, close to 300 users across Pretium are using real time information in Guidewheel every day to manage both key operating metrics and energy use of machines across all of their production locations.
Now that they have full visibility across their footprint, the Pretium Operations team is able to benchmark facilities and share best practices. They can easily identify data-driven ways to reduce energy consumption and make their operations even more efficient, then accurately prioritize the ROI of those opportunities with standardized information across their global footprint.
As just one example, the team at the Pretium plant in Paris, Illinois, USA utilized the detailed energy consumption data from Guidewheel to undertake a comparative study on energy consumption across similar machine models. The goal of the study was to analyze which machines would both improve production and reduce their total cost of power per unit produced, which is a meaningful cost driver for their business.
As they sought to deliver the best possible value to their customers alongside the best possible efficiency, the Pretium team was able to pull a variety of important information shown in the table below. Having the Guidewheel system across all their plants and machines meant that it took under three minutes for their team to pull the up-to-date energy data required for this analysis:
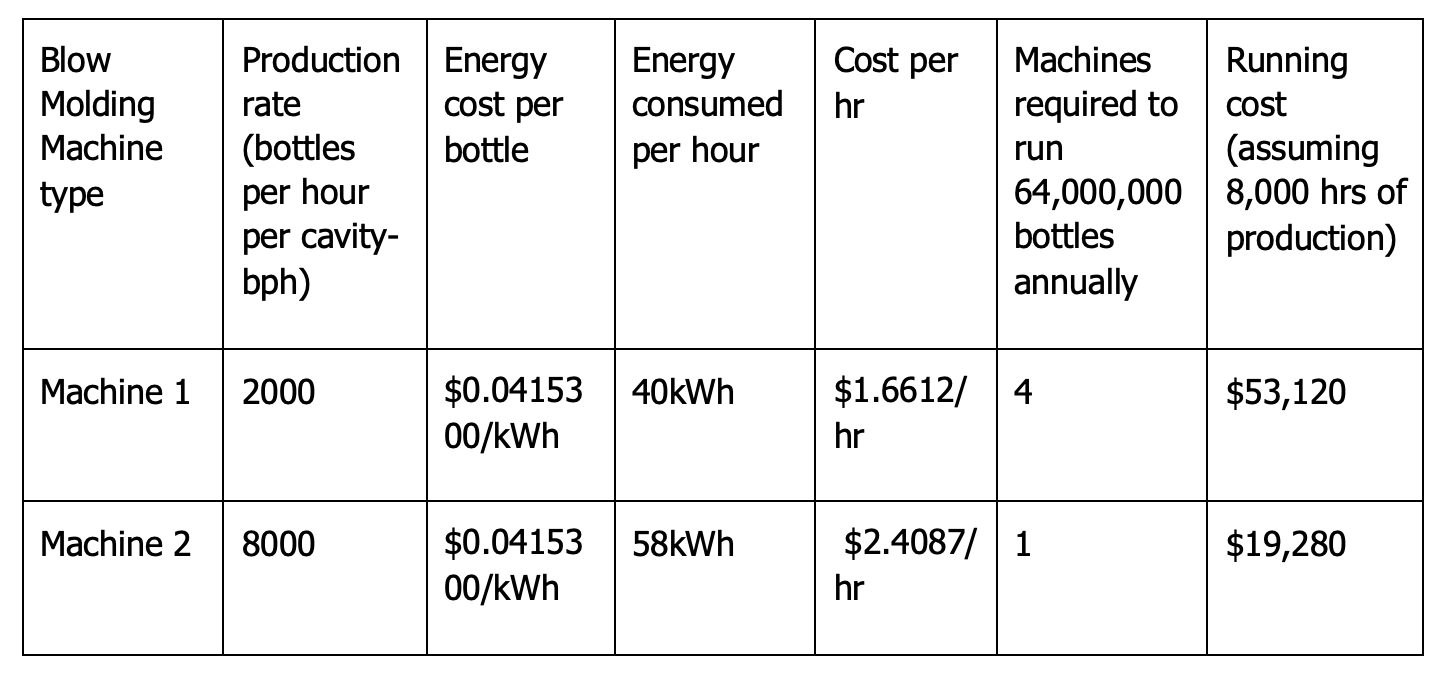
The Pretium team quickly saw that to produce the same quantity of bottles, they would have to spend nearly 3 times more in energy cost on a 2 cavity mold machine over an 8 cavity mold machine. They were able to run the numbers and compare different factors in a data-driven way to make key decisions that would be best for both their operational costs and their customers.
This is just one example of the data-driven approach Pretium is using to continually increase the sustainability of its operation. It also illustrates a few best practices:
- Using one tool to manage both key operating metrics, such as machine runtime and production, as well as energy, engages more users across the organization than having separate tools and therefore supports greater impact. When tools are separate, fewer teammates know of their existence and are able to quickly pull and use data to inform decisions. FactoryOps platforms like Guidewheel that provides a single pane of glass for both operations and energy increase the prominence of energy information within daily operations and therefore make it easier for sustainability to be prioritized in both day-to-day as well as quarterly or annual decision making.
- Having complete and standardized data across the operation enables confident decision making. Pretium identified that a major strength of the Guidewheel tool is that it works on all of their machines—old or new, across all makes and models—which empowers Pretium to run meaningful analysis across all their machines and schedule the most efficient lines for production.
- Data should be granular enough to support the best decision. For example, in the specific instance shared above, it was critical to have energy data not just for the plant overall, but broken down by machine. Without good data, misconceptions can result in less effective decisions. For instance, there is often a misconception in the industry that larger machines will draw more energy. With data, Pretium was able to easily show that this misconception did not apply in this case. They quickly identified that the smaller 2 cavity machines are not as energy efficient as a bigger 8 cavity bottle machine. All of this helped Pretium accurately understand and determine the true ROI on different investments.
- Ease of data access matters. Above and beyond the principle of using data to make the best decision, being able to quickly and confidently pull that data made the decision making process much faster. With the Guidewheel platform, energy data was at the team’s fingertips in a platform they were already using to manage their daily factory operations. Since the team utilizes the platform daily, it took less than 3 minutes to obtain detailed energy consumption data by machine, which previously had been unavailable to them.
In addition to this specific example, having energy data readily available has helped the Pretium team more generally analyze which machines will be a better use of time and resources not just for them to run a sustainable and efficient operation but to also serve their customers better. Based on both energy consumption and key operating metrics, they can schedule their machinery efficiently based on the orders and materials/labor resources they have at hand. They can also see and receive alerts in real-time if a machine is starting to fail, as machines will frequently start to draw more energy when they are having problems. Combining these core operational, energy, and predictive maintenance applications in the same platform continually empowers their team to make the best possible decisions with all factors in mind.
Pretium is now able to drive continuous improvement, informed by accurate data across their entire operation, towards more data driven, sustainable operations.
Broader insights:
More broadly, Guidewheel’s experience working with more than a hundred manufacturers in this area has reinforced that to have the greatest impact towards Industry Net Zero, solutions need to
a) Address the top business priorities: Solutions that tie to top business priorities (#1 or #2) are far more likely to be successful than solutions—even with high ROI—that tie to priorities farther down the list. For this reason, solutions that start by addressing core factory operations functionality (typically a top priority) and then layer on energy management functionality once the full team is already using the system often drive more results than solutions that address only one area, such as energy alone.
b) Eliminate friction and barriers to get started: Solutions need to be designed to work within the real constraints of manufacturing. They need to work well on older machines, work without IT/OT infrastructure that may not exist in all locations, and be low cost and complexity for non-experts to set up and use. As much as possible, manufacturers also value being able to test solutions first to make sure they will work for their machines and their teams.
c) Provide lightning-fast time to value: To engage the full manufacturing team and drive usage and results over time, a solution must quickly show value. There is a limited time period to engage and build momentum across the team, and solutions that don’t make the most of that window can quickly slip to the sidelines and go unused.