Taking Action to Increase Sustainability within Manufacturing
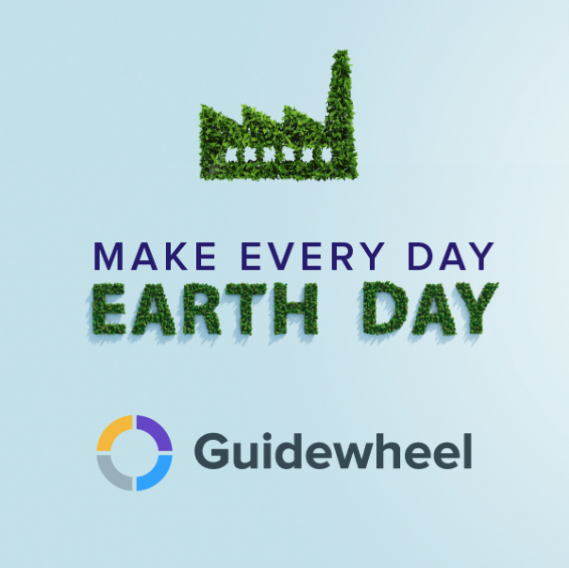
The sustainability challenge in the manufacturing industry
According to the U.S. Energy Information Administration, manufacturing accounts for 77% of all energy consumption in the industrial sector. Part of this metric is the supply chain contribution, the transportation of goods from manufacturers to consumers that causes fuel emissions from vehicles, but another significant factor relates to the processes by which goods are produced. It takes a lot of energy to run a factory and all of the equipment in it. The key to reducing that energy consumption is through advancements in technology, and the World Economic Forum argues that data-sharing is core to using those technological advancements to reduce carbon emissions. Guidewheel was founded on these same principles.
A company dedicated to improving the planet
Guidewheel was founded with a mission to empower manufacturing excellence for all factories and reduce emissions that contribute to climate change. To strengthen this mission, Guidewheel has even incorporated as a “Public Benefit Corporation” (PBC), a for-profit company with a strong social mission, to build its intention to support societal values into its foundation. Other Public Benefit Corporations include Method, Kickstarter, and Patagonia among others.
Energy management: You can’t fix what you don’t measure
Guidwheel’s FactoryOps software is appealing to customers because it allows them to gain real-time visibility into factory operations such as machine runtime data in a way that is 100X faster and easier than other solutions on the market. From such insights, customers are able to decrease downtime and simultaneously increase productivity by 20% or more. Guidewheel starts by measuring the electrical current from machine power sources to derive runtime and machine speed. This gives manufacturers the granularity to dig into machine performance on a second-by-second basis within the Guidewheel platform, with Guidewheel helping customers make sense of this data and translate it into action and results.
In addition to runtime and other critical machine metrics, Guidewheel’s dashboards also show machine energy consumption and energy intensity in in kilowatts (kW), kilowatt-hours (kWh), or kilowatt-hours (kWh) per unit, among other measurements. Measuring energy consumption on an individual machine basis provides insights into trends and how to improve. Without measuring energy consumption, customers won’t know which machines are bad actors or where action can be taken to reduce wasted energy. And secondary benefits include the identification of other types of waste such as reduction in thermal energy, reduction of air or water leakage from boilers, and general material waste that cannot be reused or recycled.
Take action
One of the easiest ways to reduce energy consumption is to make sure non-productive machines are turned off or are in power-saving mode. When a piece of equipment is “down,” this could mean that it is idling and still consuming energy wastefully and at the manufacturer’s expense, hurting the bottom line.
If machines need to idle during changeovers, making sure changes are performed correctly and as scheduled is another way to reduce waste. To help minimize this waste, when unplanned downtime occurs or a changeover is taking much longer than planned, the Guidewheel solution can send automatic text messages to employees or managers notifying them that immediate action is needed to resolve the issue.
Furthermore, the analytics and machine learning built into the Guidewheel platform can identify trends such as particular machines or components where problems are developing. For example, the platform can help identify that a machine component, such as the motor, needs to be cleaned properly or replaced all together. A dirty motor could cause the machine to act erratically and result in unnecessary waste as well as downtime and lost output and revenue. In this scenario, information brought to light may indicate: cleaning could make the machine run more efficiently, a part needs to be replaced, or the machine itself might be old, worn-out, and not up to current regulatory codes and should be replaced. The team can use trusted data to calculate how quickly the cost to make a capital investment in new machinery will pay back with long-term gains.
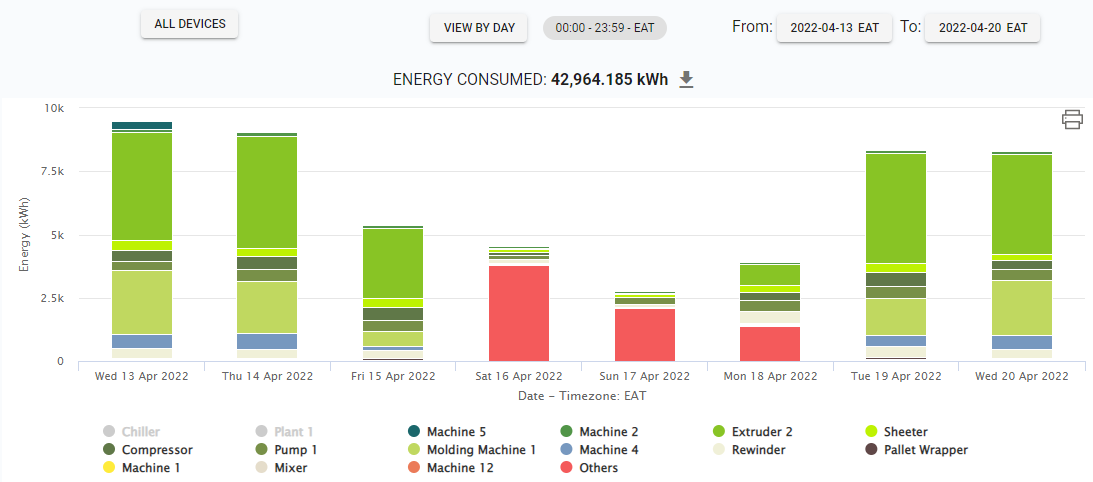
This screenshot, above, shows the energy consumption data that can be captured through the Guidewheel platform and manipulated to reveal different measurements and views to determine actionable insights.
Similarly, the Guidewheel platform can identify where machines are causing waste by being run excessively or incorrectly. For example, one of Guidewheel’s customers that manufactures paper products used Guidewheel to discover their pulpers were running in batches longer than necessary. Then, with Guidewheel alerts, the team was able to catch machines running long and reduce energy consumption by 1,045 kWh/day amounting to a total savings of $43,000/year in energy expenses.
The big picture
In manufacturing, there are many factors that can contribute to sustainability—from sourcing materials in a sustainable manner, to educating the customer about how to recycle products at the end of life. It’s a complex challenge that involves many players including the consumer to help change the word for the better. Organizations like the Ellen MacArthur Foundation have taken on this challenge, creating the concept of a “circular economy” and to encourage major manufacturers like Coca-Cola and GM to agree to net-zero emissions by 2050. Guidewheel is likewise excited to continue doing its part to help customers perform better, sustainably.
Learn more about how Guidewheel has helped customers achieve peak performance while also increasing their sustainability via these case studies.