Plastics Technology Magazine: Machine Monitoring Becomes Simpler And More Affordable Than Ever
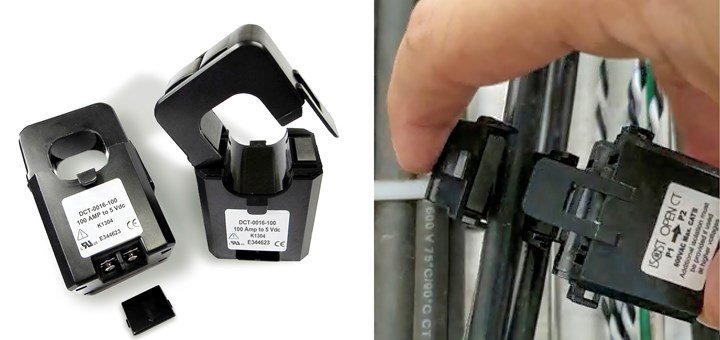
Matthew Naitove of Plastics Technology Magazine covers Guidewheel in his article about the technology waves driving the democratization of FactoryOps software, enabling mid-market factories to see significant ROI.
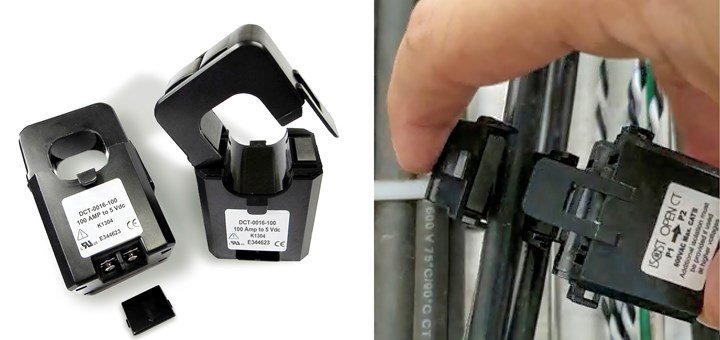
“The big story of the “industrial internet of things” (IIoT or Industry 4.0) is more than just the ability to acquire, analyze and communicate data from production systems—it’s also about the rapid “democratization” of such technology, making it available to manufacturers of all sizes, and not just the largest firms with big budgets, big engineering teams, and ample timelines for training and installation.”
Here are some real-world examples of customers that have benefited from using Guidewheel to provide run-time tracking, alerts and real-time visibility into machine activity:
• A plant with 30 extruders and thermoformers reduced production costs by 20%.
• A plastic tank manufacturer uses Guidewheel on 15 extruders, grinders and rotomolding machines. The firm achieved 37% to 62% reductions in idle time on key machines and increased facility run time by 18% overall. OEE improved by 41% in six months.
• A packaging manufacturer uses Guidewheel on its most important machines, now expanding to nine locations. It identified and eliminated 1-3 hr/day of avoidable downtime on each machine.
• Another packaging manufacturer uses Guidewheel on key machines, thereby reducing changeover times between production runs by 50% from 6.8 hr/day to 3.4 hr/day. In addition, alerts enable technicians to respond immediately to problems, and the production manager can better plan capacity across machines for faster response to customers.