Plastics News: Blazing a path toward future manufacturing through digitalization on factory floor
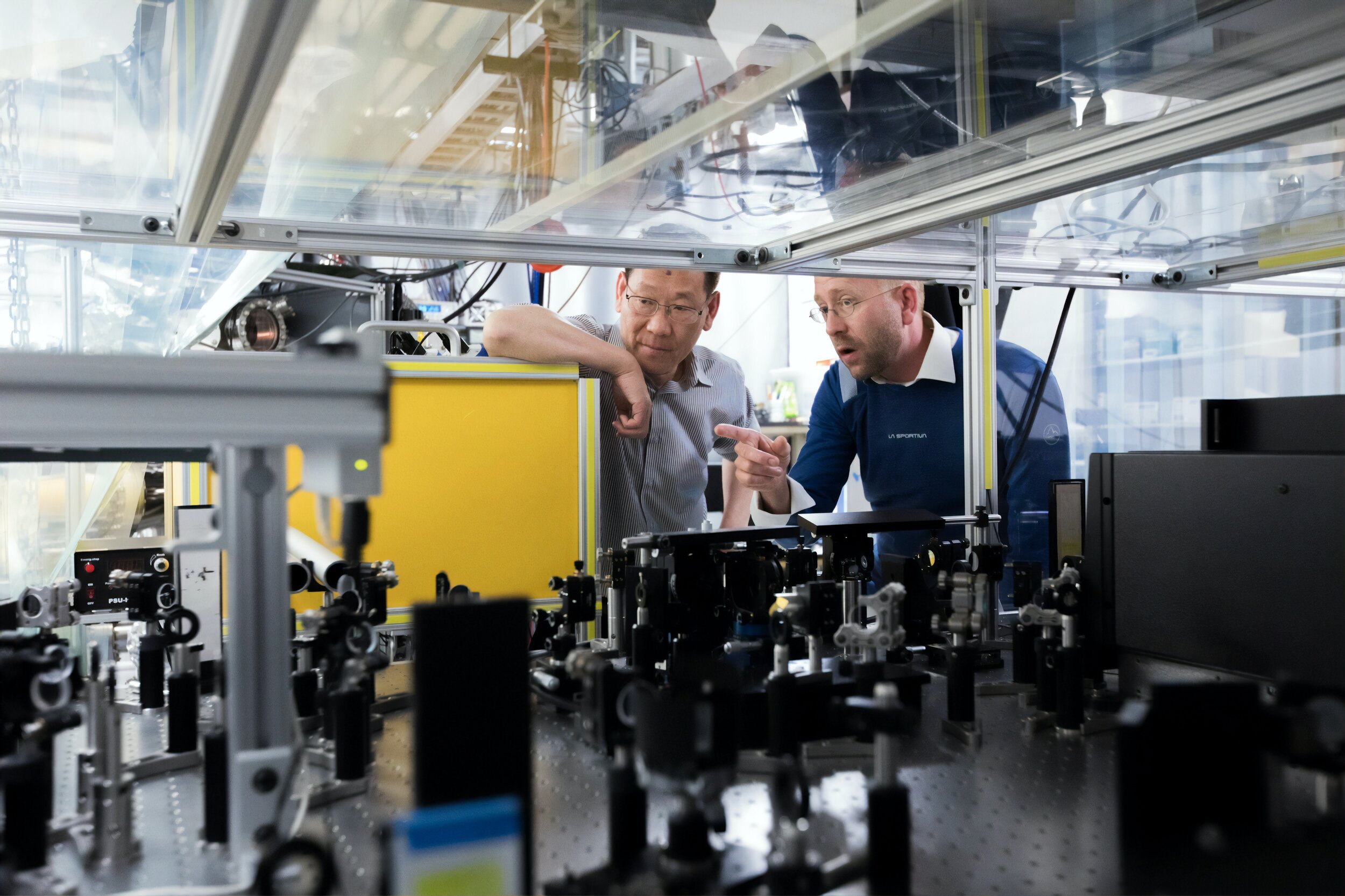
This is a repost of our article in Plastics News.
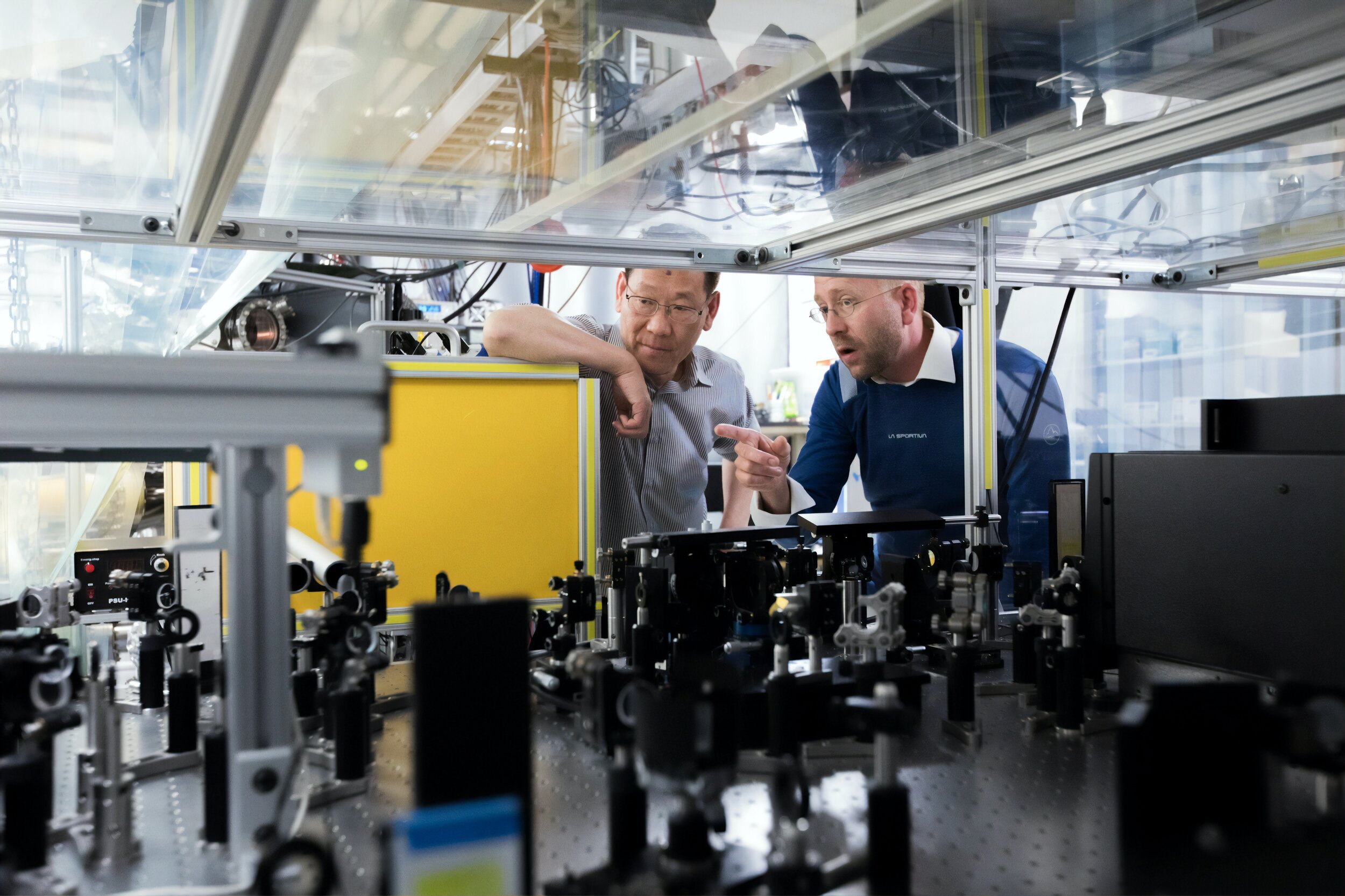
Factories have been the heart of industry for centuries, dating back to the early days of the Industrial Revolution. Many factories you see on the news appear to be the height of modernization, but the reality is, for most factories are less new and fancy.
The fact is, many factory machines were made to last for decades, so they might not need to be replaced. With older equipment that still works well, the majority of factories have a mix of equipment of varying ages, makes and models.
As a result, when the world talks about digital transformation in manufacturing, the real-life implications often seem daunting. Will we have to buy all-new machines? Replacing all that equipment could be a small fortune. And for what? If they're still working well, it seems hardly worth the investment. In most cases, replacing everything would be complicated, expensive, and completely unnecessary.
Digitization, though, is not just about the machines. It's about the way we track and manage them. This tracking and management is still a largely manual process in most factories.
We all appreciate the "machine whisperers" on the factory floor, who know the machines so well they can hear a problem from across the plant before anyone else notices, track machine health with a well-traveled clipboard and find the solution within moments of discovering a problem. A machine whisperer's job has become infinitely more challenging in today's environment. Add in more factories, a greater mix of machines, a growing labor shortage — and you're facing an ever-increasing volume of data and information in silos that don't connect, leaving teams wrestling with manual data entry and constantly putting out fires.
As a result, manufacturers typically lose more than 20 percent of production time. That's a cost of more than $3 trillion in waste each year. In an era where improving not only margins but also sustainability is increasing for plastics manufacturers all over the world, this statistic is unacceptable.
Enter: technology. When we talk about automating the factory, we still want those machine whisperers to work their magic. When you pair their knowledge and skills with the power of the cloud, the results can be astonishing.
Consider a plastics tank manufacturer, who was tracking its machines by collecting daily logbooks and entering results into a massive spreadsheet. This data took hours to compile each day. Yet after all that work, it was too "after the fact" and full of inaccuracies to be actionable in addressing machine downtime. The manufacturer decided to experiment with bringing its machines, both old and new, into the cloud.
Starting with just one machine, and working in close collaboration with the production team, they set a goal of reducing lost production time by just five minutes a day. Within five weeks, that goal was surpassed; with a reduction of three hours in average lost production time. Two months later, with all key machines in the cloud, the manufacturer has seen a 62 percent reduction in downtime.
Ultimately, enabling smart factory operations isn't about replacing people or machines. It's about leveraging technology to enhance them.
The question, of course, is how. The answer: the cloud. The cloud can bring the "heartbeat" of any machine into a centralized place to view, analyze, and optimize operations for any business. The cloud has enabled FactoryOps — a new category of technology that uses the power of the cloud to bring any machine online, into a connected network that simply and cost-effectively gives every factory team the tools to reach manufacturing excellence.
Imagine being able to view the real-time activity of any machine, anywhere on the factory floor, in one place? Imagine if one machine's heartbeat was connected to all others, creating a unified network of machines and people that can continue to learn and improve from one another?
Imagine if the factory whisperer — or a team of factory whisperers — had the right tools at their fingertips to proactively identify and take actions to improve production?
This has the potential to truly transform factory operations - without a costly overhaul. Here are three reasons why it's worth getting your factory onto the cloud:
- Get more out of existing machines. We all know the adage: Don't fix it if it isn't broken. And we couldn't agree more. Replacing machines can be extremely expensive, not only in terms of equipment and installation costs, but the time required to implement and train the team. The key is to find a low lift, high return opportunity to get your existing machines online, without replacing them outright. Adding your legacy systems to the cloud means you can not only protect previous investments, but empower your teams to further optimize them as they assess, analyze, and improve them in real-time.
- Be ready to adapt, sooner vs. later. If we've learned anything from the last 18 months, it's how important it is to be flexible in response to changing market conditions. Whether we're facing a resin shortage, growing labor constraints, or whatever the next supply chain challenge will be, technology can step in where materials and manpower may fall short. The ability to manage across all machines from the cloud makes it much easier to adjust production according to demand, improve changeovers to increase capacity to sell, and more.
- Make sustainability a reality. Sustainability in plastics is a top priority for manufacturers around the world. To achieve it, it's critical to have an energy management strategy in place. Statistically, up to 15-20 percent of a factory's assets are left unused and idling at any given time, which not only impacts run time and efficiency, but creates massive energy waste. Manual tracking and processes won't solve the problem; in fact, they often won't even detect it (remember our plastics tank manufacturer?). The cloud can offer a real-time view of idle time, run-time, and offline thresholds, making it much easier to course-correct and set achievable goals for productivity and sustainability on a global scale.
Can we get every factory in the world to sustainable peak performance? It's a lofty goal, but the cloud can go a long way in helping us get there. New advancements in friendlier technology mean no one has to be afraid to embrace it.
Lauren Dunford is the co-founder and CEO of Guidewheel, a plug-and-play FactoryOps platform that brings any machine online into a connected network.