Case study
Nice House of Plastics reduces weekly idle time by 67% with Guidewheel
Updated:
September 21, 2022
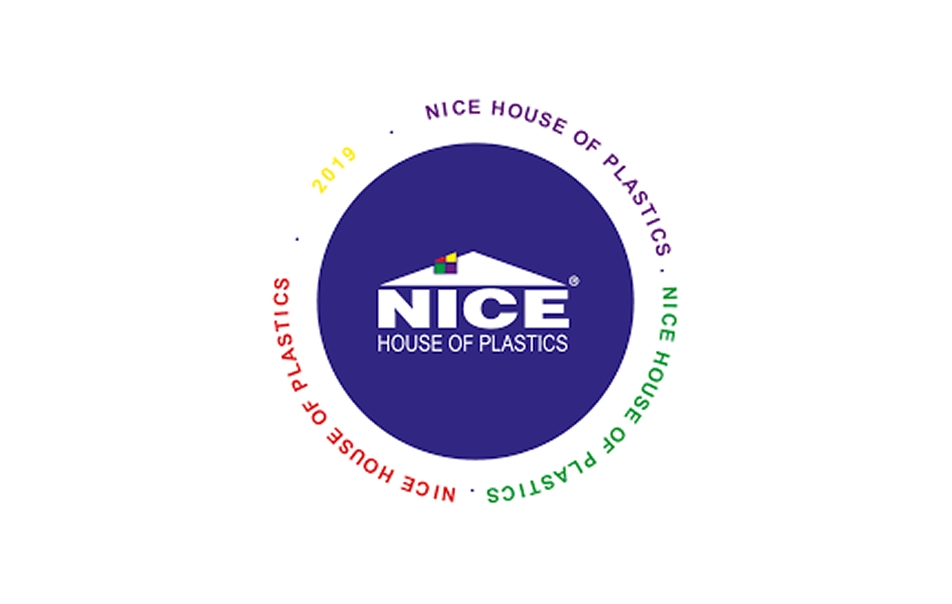
Nice House of Plastics Limited are proud to be a manufacturer of household and industrial plastic items. The company was founded in 1970 by Dr. James Mulwana, a leading entrepreneur and industrialist. He strived to create the base that has since grown to become well-known across East Africa. The Nice House team has worked diligently to offer unmatched professional expertise that has made them the most trusted provider of plastic products in their region.
Eddie Senkumba, Head of Operations at Nice House of Plastics, brought on Guidewheel to save energy, improve production efficiency and empower his team with realtime information on the production floor.
Early this year, Eddie and his team began focusing on using Guidewheel to track equipment idle time. Their goals in focusing on equipment idle time were twofold. They wanted to:
- Improve production efficiency. Times when machines were idling typically correlated with setups, changeovers, or other times that could be shortened through optimization in order to increase total production per shift. The team was interested in applying continuous improvement best practices to increase the efficiency with which they used available hours for production, thereby improving labor and resource efficiency.
- Get clear insights into opportunities to reduce energy consumption and cost. Machines idling when they were not being used were drawing expensive energy without contributing to production, so the team wanted to see if they could reduce idling times to reduce the cost per unit of production.
Eddie and his team started by using Guidewheel to evaluate the baseline for their production process. In February 2022, they established that the cumulative baseline for the 15 machines in the first plant they evaluated was 1500kWh/week.
Next, they focused on applying continuous improvement and measuring the results from that baseline. Nice House of Plastics and Guidewheel partnered and led a series of weekly reports and trainings for the team on how to use and take action from information from Guidewheel.
They started applying the following process in their team meetings to align the team around improvement:
- In regular weekly meetings, they pull up the Guidewheel weekly report
- Then, the team reviews the list of equipment with Overall Equipment Effectiveness (OEE) of <50%.
- For each piece of equipment with OEE <50%, the team reviews the data on why OEE was lower than expected.
- They focus on the most important equipment, and on major recurring issues that cause long instances of disruptive downtime.
- Then they specifically pull up idle time per machine, translating that time into the cost of that idle time — which is motivating for the team because it represents wasted money that, if recaptured, could be spent on other things to drive the business.
- In addition, they make sure to celebrate improvements from previous weeks, and identify learning that can be gained from those improvements.
On the plant floor, they focused on two areas in particular to positively impact both energy cost and productivity:
- They focused on using the Guidewheel system to automatically track issues, with the team using the system to acknowledge and close issues so everyone can stay on the same page, ensure timely response, and easily see which problems are causing the greatest impact.
- They changed the process so that when equipment is not scheduled to run, it is switched off rather than remaining idle unless there is another batch waiting.
With those actions, Nice House of Plastics was able to:
- Reduce downtime due to changeovers (mold changes) from hours to minutes depending on the process being produced. This has improved their production efficiency as well as flexibility.
- Also lower the amount of energy used by idling machines to consistently average less than 500kWh/week, a savings of 1000kWh/week. This translates to an annual saving of 52,000kWh/year or approximately $4,644 annually.
This success is just one example of the operational changes that Nice House of Plastics has been able to drive through the partnership with Guidewheel.
As the team continues to expand their partnership with Guidewheel and get even more value, the true measure of success is the excitement and buy-in from the entire team: The operators on the floor asked for Guidewheel to be expanded into other areas of their operations so they could benefit from the increased visibility and collaboration through the system in even more areas of production. This team-led expansion is a great testament to all levels of the company.
With the broad support and motivation from this dedicated team, the road ahead is certainly likely to be filled with even more success stories.
Our thanks to Eddie Senkumba from Nice House of Plastics for sharing his experience highlighted here. If you and your team would like to showcase how you are using Guidewheel to drive business results—or don’t yet use Guidewheel, but would like to!—send us a note at info@guidewheel.com.