How Machine Monitoring Impacts Your Bottom Line
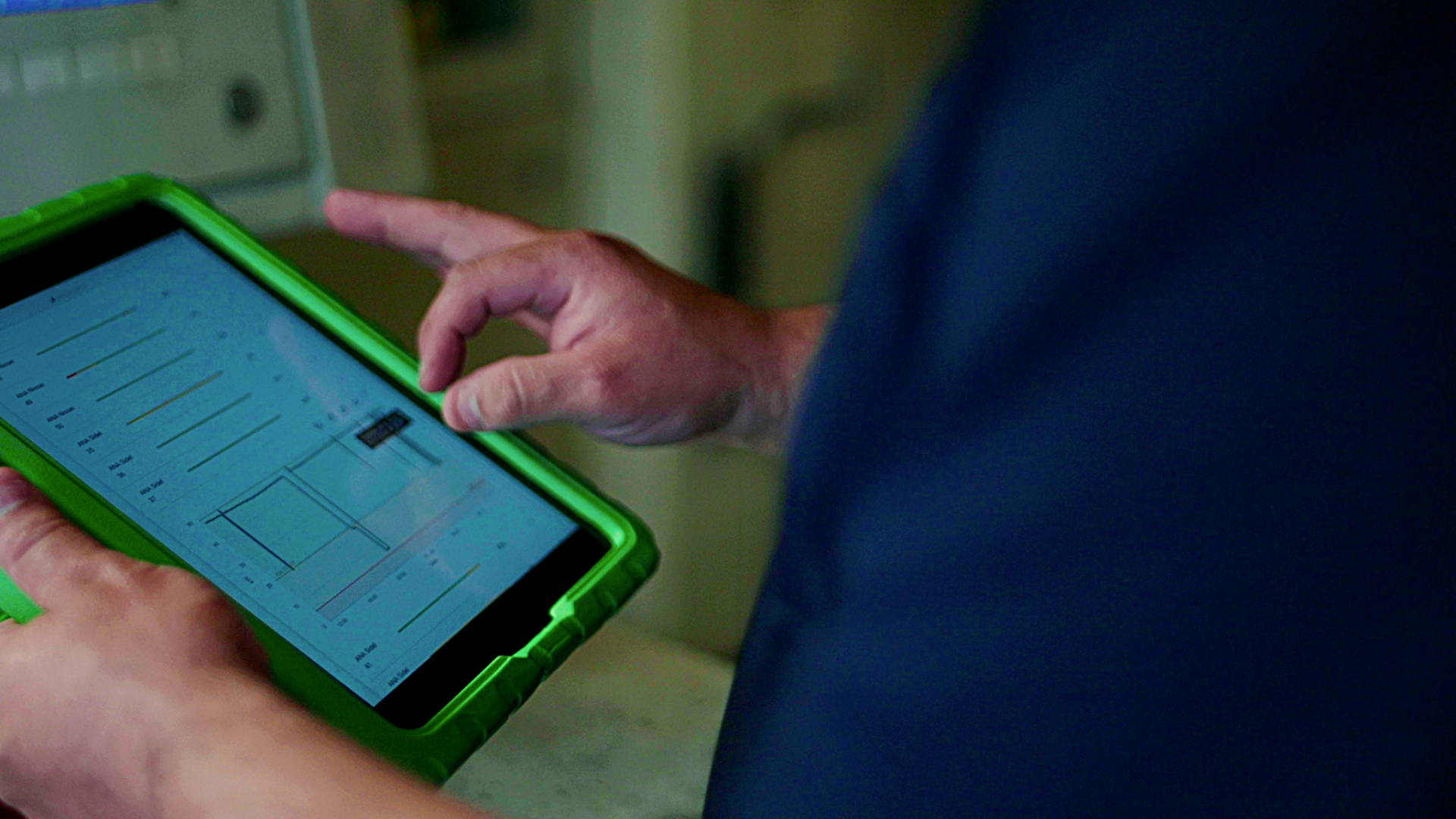
Manufacturers are under a lot of pressure these days. Economic uncertainty, supply chain issues and talent issues continue to put strain on operations and make what is already a challenging job, just that much harder. What makes it even more difficult is that most manufacturers are still dealing with manual systems that make it difficult to get the information they need to make the right decisions at the right time. Resources get allocated to the wrong problems, people are reliant on gut feelings, and the data that is available is either siloed, or not trustworthy. In order to understand what is really happening on the factory floor, many manufacturers are looking at machine monitoring solutions to help them pinpoint where they can make improvements that will actually improve their bottom line.
What is machine monitoring?
Machine monitoring allows manufacturers to capture data about machines which can then be analyzed through software to give them information on things like downtime, utilization, machine status and energy consumption. By using sensors attached to the machines the data can be transferred to the internet which allows real-time production monitoring and analysis of production data.
How can operations leaders use machine monitoring?
By capturing data in real-time and making it instantly available to anyone with a connected device, operations leaders can shine a light on all areas of production and see exactly what changes they should make. This can have a significant impact on the bottom line.
Reducing CapEx
By understanding exactly what capacity you have, better decisions can be made about when you need to purchase new equipment. Once a machine monitoring solution is installed, most manufacturers quickly realize that they have a lot of untapped capacity in their existing machines and are able to quickly get more from what they have instead of making new investments.
More efficient use of labor
Overtime happens. But are you sure your teams need to do it as often as they are now? By understanding exactly why your machines are down, putting new solutions in place, and utilizing automated alerts, teams can often find ways to get more done in the regular hours of the day instead of constantly going into overtime because of machines being down.
Identifying lost revenue opportunities
For manufacturers that are capacity constrained vs. sales constrained, realizing that you have more capacity for your sales team to sell into is a great way to increase revenue without significant investments.
How do you get started?
Monitoring downtime is the first and most important step. If you’re looking to progress towards fully automated production data analysis, taking a crawl, walk, run approach will get you quick wins that hit the bottom line very quickly. If your machines aren’t running, they aren’t making you any money, so starting with downtime allows you to quickly identify the ways you can increase your revenue streams and/or reduce your costs. Once you’ve ‘turned the lights on’ and have a single source of truth for everyone to work from, you can start to introduce more sophisticated processes like systematized alerting and continuous improvement.
How easy is it to get a solution in place?
Many manufacturers have had false starts with machine monitoring solutions, or trying to utilize existing technology to get real-time visibility as well as all the other benefits they are supposed to provide. But new technologies have made this a quicker and easier process, that doesn’t require lengthy IT projects, or massive change management. FactoryOps solutions are now harnessing electrical current data, combined with new cloud-based software solutions that can be deployed remotely in a matter of days. The advantage of this approach is that the age, make or model of the machines doesn’t matter - all equipment can instantly be tied to the same system and allow visibility across the entire plant, or even multiple plants. By presenting digestible data that anyone can understand, manufacturers can make improvements quickly because everyone has the information they need, not just a mountain of data.