Case study
Real-time visibility to achieve 50% downtime reduction: 6.8 hrs/day to 3.4 hrs/day per machine
Updated:
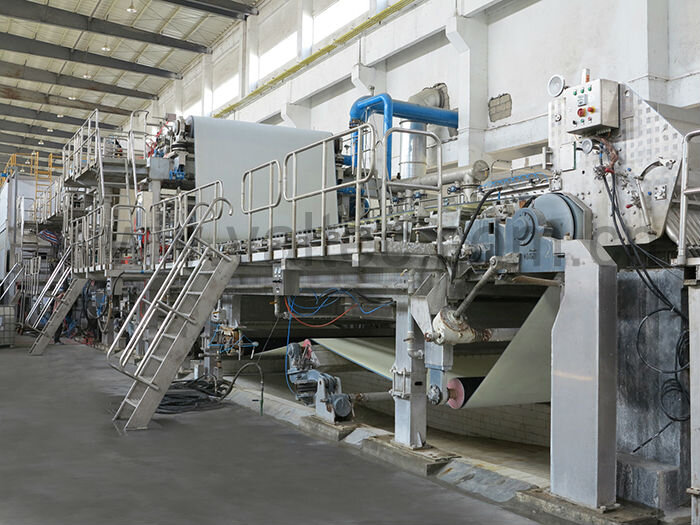
After decades working in the factory, the production manager knew his five most critical machines like the back of his hand. In addition to having deep experience within the packaging industry, he had spent most hours of each day around these same important machines for years and could easily tell what was normal, and what was not. He could even predict what a typical run should look like.
His interest in getting real-time visibility was not driven by a lack of understanding of his machines, but rather, the desire to move away from pen and paper to digitized systems that could provide a shared source of truth across the team. He was proud of his team and eager to support them in hitting their targets. He also thought visibility might support his team in sharing best practices across shifts, as some machines showed variability from shift to shift depending on the operator.
After the production manager described these areas of interest, the Guidewheel team worked with him to conduct an assessment of processes and key bottleneck areas and get the system set up on his equipment. For his first time logging into the Guidewheel system, he opened up his laptop not in the boardroom but in his office on the first floor, where he could physically see what was happening on the factory floor. To ensure that he fully understood the Guidewheel system in the same way he understood his machines, he had one of his Operators on standby at the factory floor to compare the data in the Guidewheel system to the activity of the machine at that moment. He asked the Operator to switch the machine off, switch it back on, load the machine, run it on different speeds, all the while observing the corresponding changes in machine behavior on the Guidewheel system. This confirmed alignment with everything he had come to understand about each of the machines over the years. It also gave him the confidence to make Guidewheel his single source of truth for performance analysis.
Having a cloud-based system added tremendous flexibility to the Production Manager’s daily routine. Suddenly, he no longer had to be on the factory floor to know what was happening. For example, he started using the Guidewheel system to provide remote support for the night shift. Even when he was at home, he could have perfect visibility to what was happening to answer any questions and provide advice in real-time.
Each morning when he arrived at the factory, he pulled up each machine’s chart in the Guidewheel system, identifying any machines that did not meet their targets. He then sat down and reviewed with the relevant shift leaders the reasons why and what measures they could take to mitigate against future occurrences. He was able to get crystal-clear visibility into downtime for the first time, and saw he was losing on average 34 hours/day in unplanned downtime across his five machines - an average of 6.8 hours/day per machine. Looking at that large amount of production time lost - time when the plant could be making revenues - he and his team felt an urgency to take action.
Prior to Guidewheel, the production manager had been tracking machine OEE on Excel spreadsheets. But with the system providing automatic OEE calculations, he saved time on data entry. Rather than spending hours inputting numbers, he was able to focus his time on analyzing the data and drilling into machine level performance - something he had previously lacked the time to do. He had more time at hand to plan forward and support his team in implementing necessary changes.
Once a month, the production manager pulled his own monthly reports from the system for more detailed analysis, which he shared with his Finance Director to align on overall goals for the coming month. Soon, the Finance Director also grew more interested in what Guidewheel could do for the Finance department. He started to depend on Guidewheel for visibility into issues that were affecting production and causing them to miss targets. He started to use this data to align with relevant teammates on the operations side and put in place additional measures on the purchasing, planning and materials side to reduce downtime.
Simultaneously, the Production Manager worked with the Maintenance team to set up real-time alerts in Guidewheel so they could know immediately when something was wrong with a machine. Rather than relying on someone to call them when there was a breakdown - with the visual monitoring and phone tag frequently resulting in delays - they could count on getting immediate SMS alerts and the tools they needed to diagnose the issues from their phones no matter where they were physically located. This helped them significantly improve their response time, and allowed them to proactively conduct preventive maintenance and stay on top of their machines as a team instead of constantly firefighting and being on the back foot.
Over the course of five months, the team worked together across these three departments - production, finance, and maintenance - and was able to reduce downtime across their five machines from an average of 6.8 hours/day per machine (34 hours/day lost across the facility) to 3.4 hours/day on average (17 hours/day lost across the facility). This 50% decrease in lost production time translated to substantial increased throughput, and in turn, increased revenues and margins. A win for the entire company.