Automatically track duration of issues that may be holding you back
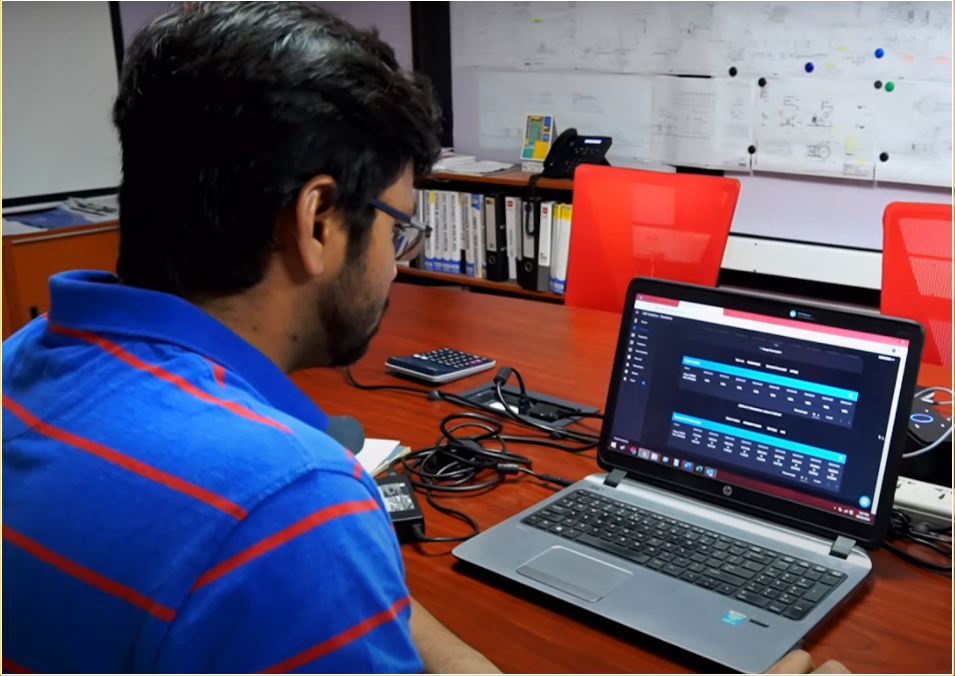
new features in Guidewheel help automatically track and prioritize causes of downtime
Manually measuring downtime can become tedious. Instead of struggling with a stopwatch, Excel, or a notepad, Guidewheel now has new features to help you track and prioritize causes of downtime automatically.
Use Auto-resolving alerts to automatically measure downtime duration.
You can use Guidewheel’s Auto-resolve alerts to automatically tag and track duration of machine downtime for easy access and analysis later. All new Alerts in Guidewheel include the Auto-resolve capability, and you can also update existing Alerts to Auto-resolve.
For instance, you may care about improving run-time on your Extruder. You believe there are opportunities to optimize Setup for different Extruder runs, and that keeping Setup times close to ideal will minimize costs from lost production time. Auto-resolve Alerts can help you automatically track these Setup times, formulate a goal based on the possible amount of run-time improvement, and track progress towards that goal. To set up the right Alerts, you may know that the Active Power of your machine during downtime is between 5 kW and 10 kW. On the Issues page under the Alerts tab, you can create an Alert that is triggered when your machine’s Active Power is within that range to measure how long the machine was in downtime. In the Alert popup, make sure that the Auto-resolve box is checked so that the duration of the Alert condition can be measured automatically. Also remember to include a tag like “Setup” so the data collected can be viewed later with other similar incidents.
Once the conditions of an Alert are no longer met, the Alert will automatically resolve itself, record the time that it has been active, and tag the new data. In our example above, if the machine starts running again with an Active Power of above 10 kW after 30 minutes of downtime (between 5 kW and 10 kW), the Alert will resolve itself and record that it has been triggered for 30 minutes. When you look at the list of Alerts, you can easily see that the machine’s downtime took 30 minutes based on how long the Alert was triggered. Now, you can quickly locate all of the resolved and unresolved Alert Durations on the Issues page to analyze specific incidents. Additionally, with the “Setup” tag you attached earlier, this new data will be combined with other “Setup” data so you can later analyze all instances of Setup downtime together.
Auto-resolve’s ability to measure the duration of certain incidents can help you manage machine activity without having to manually scan for incidents and record their times. Another way to utilize the durations on the Alerts page is to sort issues by duration by clicking on the column title “Duration”. Sorting issues from by duration can help you prioritize which machines need your immediate attention.
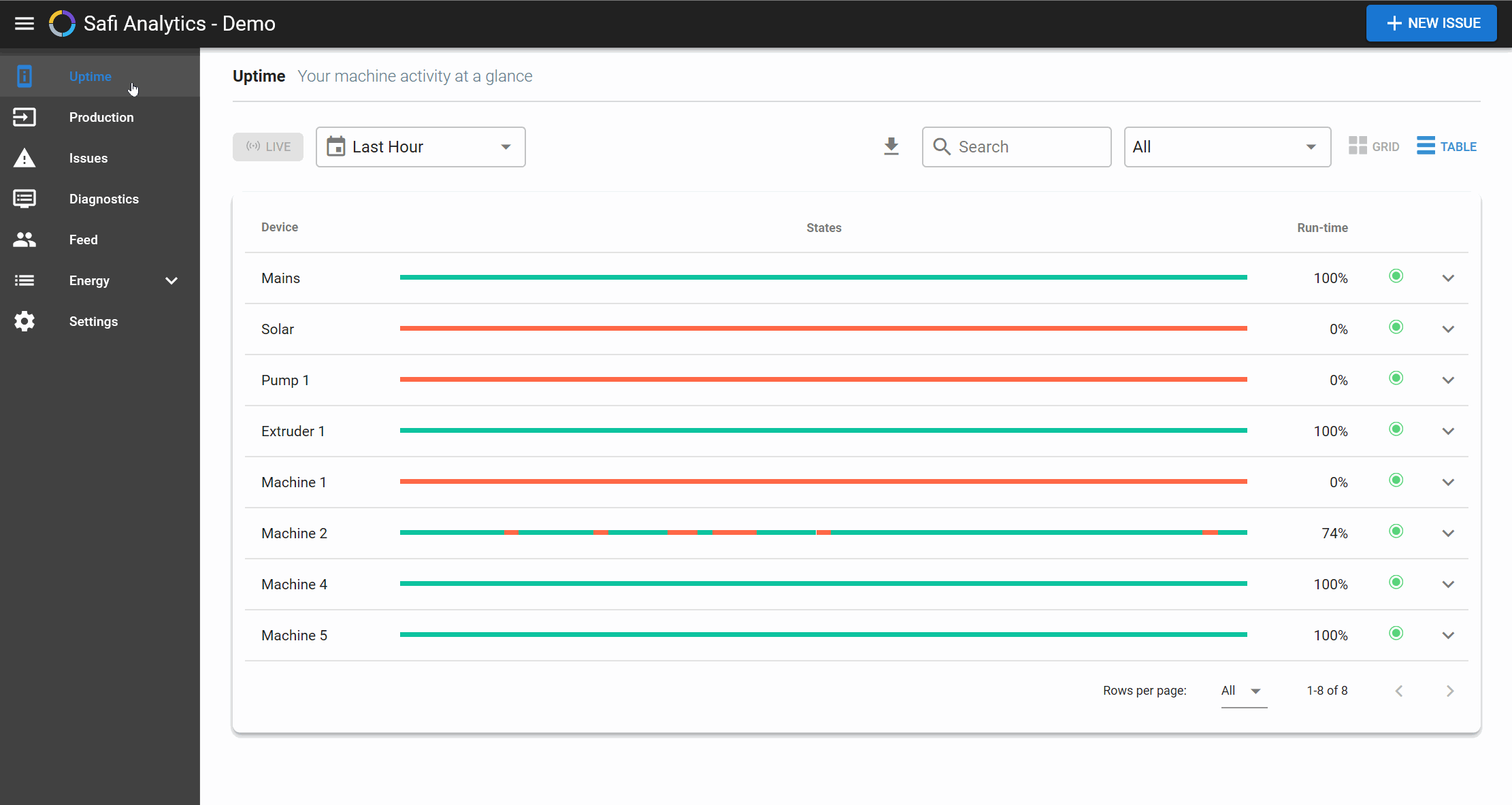
Trigger Alerts only when you need them
The new Alerts page to be released next week also has improved “Do Not Disturb” capabilities. On the bottom right quadrant of the Alert popup, you can customize what specific days and times when you do not want the Alert to be triggered. Continuing from the example above, if you only want to know about a machine’s downtime during a specific shift, say, to find the source of a recurring issue, set the Alert to “Do Not Disturb” for all other times. With Auto-resolve, the Alert’s duration will be recorded if it is indeed triggered at some point during the shift. However, the Alert will stay silent even when conditions are met outside of the time: if the machine was on downtime in the middle of the night when the Alert is set to Do Not Disturb, the Alert would not be triggered.
Setting shift times can be as simple as clicking the Do Not Disturb icon next to the days of the week when you’re off. To set a more specific time period, enter the start time when you do not want Alerts to be triggered, then set the end time. If the start time overlaps the end time, the end time automatically rolls over to the next day so the Alert won’t be triggered overnight. For example, if you set Do Not Disturb on Tuesday to start at 8 p.m. and end at 8 a.m., the Alert will not be triggered for the 12 hours between 8 p.m. on Tuesday to 8 a.m. on Wednesday.
Using a mix of Auto-resolve and Do Not Disturb can help you more efficiently pinpoint and prioritize issues throughout the day and maintain a record of issues throughout longer periods of time.
If you find additional creative ways to use Guidewheel to make your factory more productive or efficient, please don’t hesitate to contact us at info@safi.ai. We love hearing how the system is helping you increase your productivity.