No items found.
blog
Best practices to reduce changeover time
By: Guidewheel
Updated:
July 1, 2020
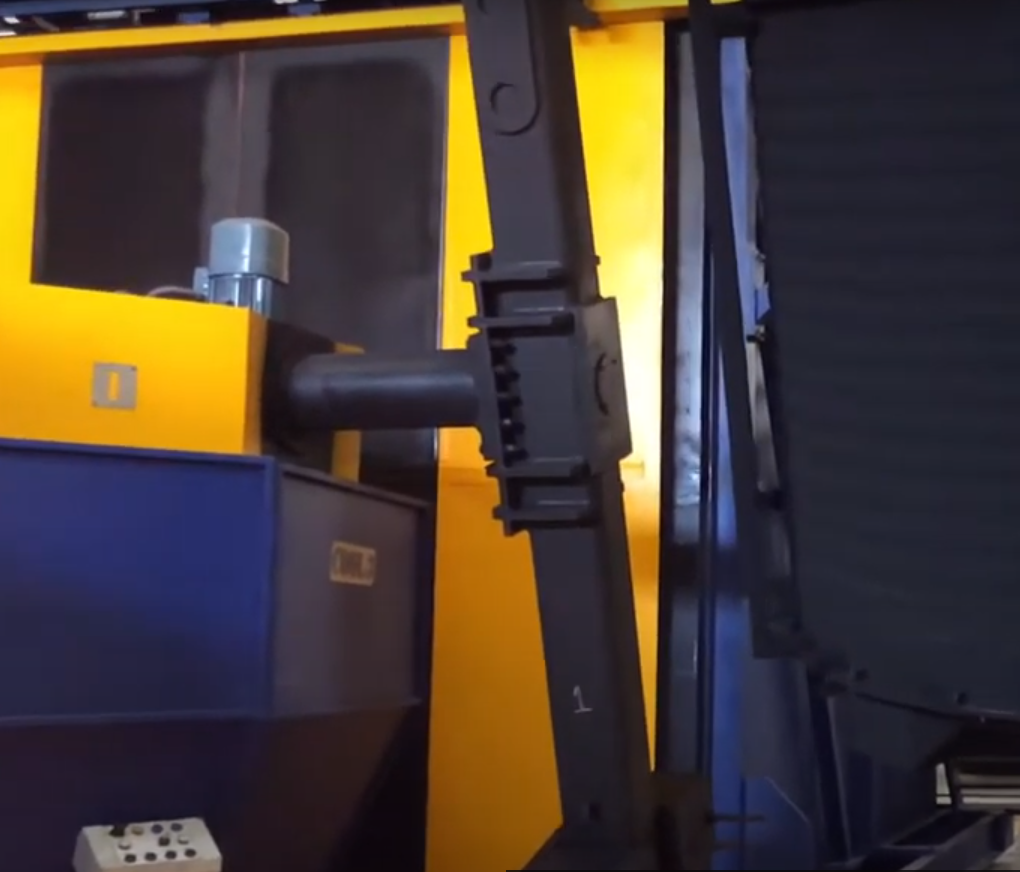
Long changeover times can be an important cause of lost production time and low efficiency in manufacturing. Optimizing changeover times can help streamline plant operations and maximize productivity.
Here are five best practices as you streamline changeovers:
- Ask the operators themselves if there is any way to make setup easier and eliminate lost time during changeovers. Explore ways to share general strategies or specific ideas used by those who achieve great changeovers.
- Once you have determined best practices, standardize the changeover process across all similar machines, allowing operators to follow a single process and for best practices to be applied and improved across the team. Standardizing the process also provides an additional opportunity to identify and address bottlenecks.
- Use checklists to keep track of important items and to make sure that nothing falls through the cracks during changeovers.
- Have everything ready for the next operator, keeping all tools or essential parts in a close and easy-to-find location, to speed up the setup process after each changeover.
- Look for ways to minimize the overall number of changeovers by dedicating certain machines to certain tasks or combining parts of the manufacturing process.
If you would like to suggest other best practices, let us know via Twitter, Facebook, or LinkedIn.
Sources, and to learn more:
Top 14 Ways to Reduce Changeovers in Your Plant
3 Best Practices to Reduce Changeover Time
How to Reduce Changeover Time with Standard Work Instructions