Setting and reaching goals
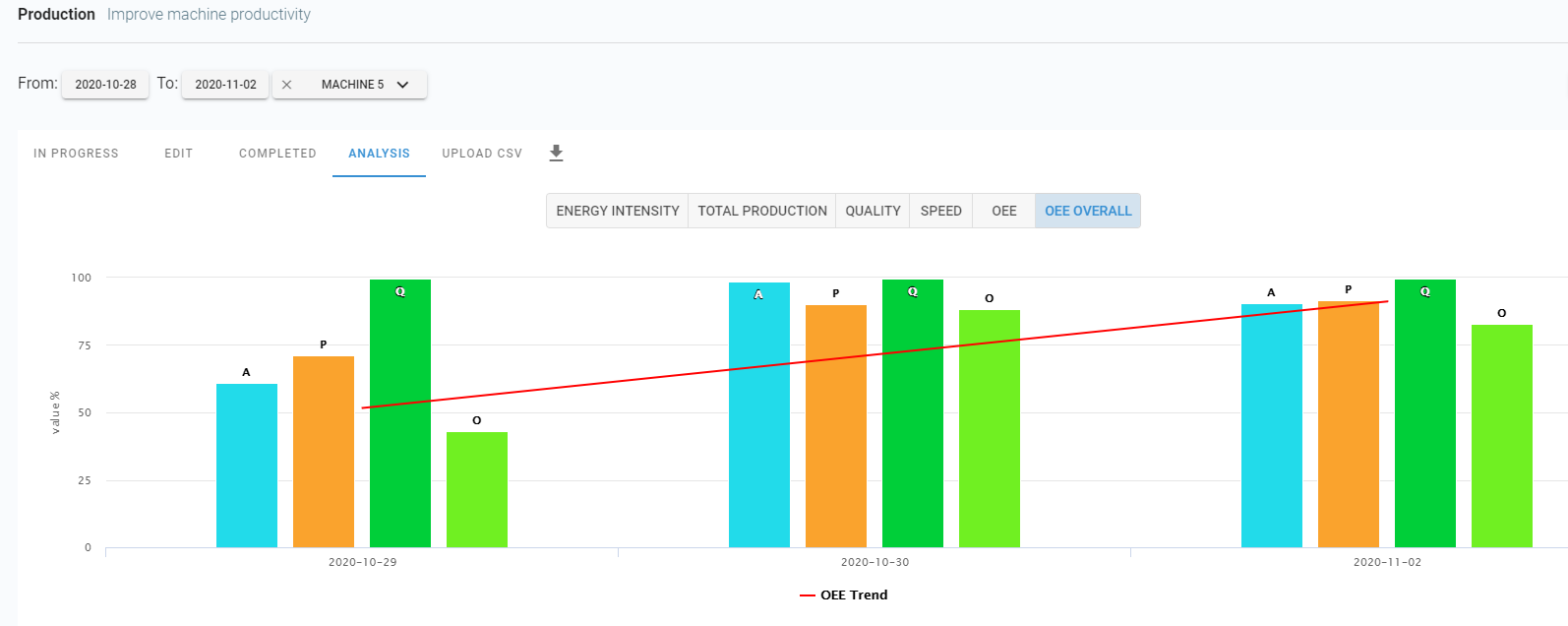
If you’re a plant manager who wants to improve production, chances are you have set goals for your team before. However, real life will often not go according to plan. Consider trying some of these tips to help you set reachable goals, figure out where to start, and get closer to making your goal a reality.
Goals should be backed by data.
Dreaming about what you want your plant to look like in the future is a great exercise to keep your goals in mind. To reach these lofty goals, you can take your first steps based on what your team and machines can realistically achieve in a certain amount of time. Every few weeks, you can take a look at your records to find the most efficient run-time for each type of machine, then set a goal to get all other similar machines up to that level. If you use a platform like Guidewheel to record and analyze data, you can use the “Previous Best” feature to identify achievable goals. Setting a reachable goal makes it more likely that you will achieve it and boost the team’s motivation to take on the next target.
The more specific the goal, the easier it is to measure.
Maybe you’ve come up with a goal to increase production by 10%, but halfway through the process you can’t see any progress. Perhaps you found that only looking at OEE at the end of the day wasn’t enough for you to figure out what was slowing down production. In most cases, coming up with a more specific goal focused on one machine shift will simplify tracking progress and troubleshooting. For instance, instead of a goal to increase production, try something more specific like decreasing the changeover times of Extruder 2 to under 25 minutes, or having a maintenance teammate at the machine within 10 minutes of any machine failure. Furthermore, specific goals result in smaller projects that can be delegated to the operators working on the machines you are targeting, engaging the whole team in reaching the same goal.
Progress towards goals should be measurable.
You have a goal in mind. Now, you just need to figure out if your team has been getting closer to your goal. Before starting a project, you can come up with a plan to record progress using metrics like OEE, uptime, or downtime (check out our post here for more metrics you can consider). The clearer the result can be shown visually, the more motivating it is! You can showcase results using graphs, charts, or before and after stats.
Encourage top level management to endorse goals.
Through our experience working with many different manufacturing teams, we have heard that companies where everyone knows and is moving towards the same goals tend to reach their targets much faster. That means everyone, from the executive to the operator, is aligned and knows exactly what needs to be accomplished each day. When top-level managers who may not normally be involved in everyday operations endorse goals or publicly reinforce the progress that has been made, the whole team will feel more unified.
With an inquisitive mindset, a drive towards improvement, and great goal-setting skills, even issues you thought were permanent can often be fixed. Try to always keep in mind the goal your team is trying to achieve. It might mean writing it on the dashboard in bold letters. Additionally, if you choose to use software like Guidewheel, invest the time to learn its features and input your production data so that you can gain the most out of it.
If you have questions, comments, or suggestions about Guidewheel or future posts that could be helpful, please don’t hesitate to get in touch at info@safi.ai.